Warehouse Pallet Racking Systems
Optimising warehouse operations begins with one critical decision: choosing the right pallet racking system. Whether you're scaling your storage capacity or improving inventory access, having a well-planned racking solution is key to using your warehouse space efficiently. At uTenant, we connect businesses with tailored warehouse pallet racking systems that meet Australian standards and streamline operations from the ground up.
Why Your Business Needs the Right Pallet Racking System
A well-designed pallet racking system isn't just about storage—it's a fundamental part of how your warehouse functions day-to-day. From improving accessibility to enhancing safety and maximising available square metres, your racking system should support both your inventory profile and operational flow.
Benefits of a Quality Warehouse Racking System
- Optimises warehouse space for better inventory turnover
- Supports safer, more efficient warehouse operations
- Offers scalability to grow with your business
- Ensures compliance with Australian Standard AS4084
- Reduces downtime and improves picking speed
Whether you're handling small fast-moving goods or bulky, palletised stock, uTenant can help you match the right system to your exact storage needs.
Types of Pallet Racking Systems
Every business has different requirements, which is why we stock an extensive range of pallet racking solutions. Here's an overview of the most common systems available in Australia today.
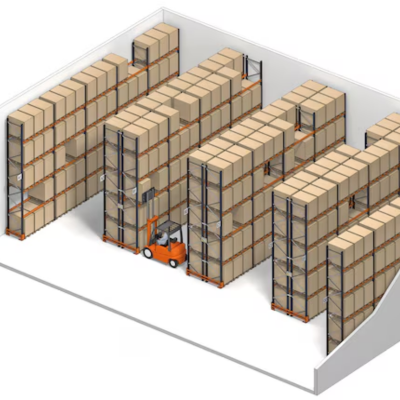
Selective Pallet Racking
Selective pallet racking is one of the most popular systems in Australia—and for good reason. It provides easy access to every pallet, making it ideal for high-turnover inventory or operations requiring fast order picking.
Features:
- Individual access to each pallet
- Simplifies stock rotation
- Compatible with a variety of forklifts
- Suitable for LIFO inventory management
If you need flexibility and visibility across SKUs, selective racking is a reliable and cost-effective choice.
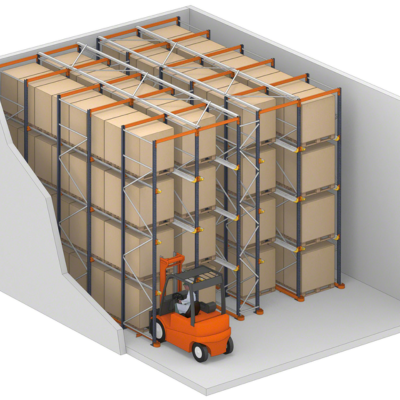
Drive-In and Drive-Through Racking
These warehouse racking systems are designed for high-density storage, particularly for products with longer shelf lives or fewer SKUs.
Drive-in racking supports LIFO (last-in, first-out), while drive-through racking allows FIFO (first-in, first-out), offering pallet access from both sides.
Benefits include:
- Maximised storage with minimal aisle space
- Best suited for homogeneous goods
- Excellent option for bulk storage
Drive-in racking can significantly increase your cubic storage capacity without expanding your footprint.
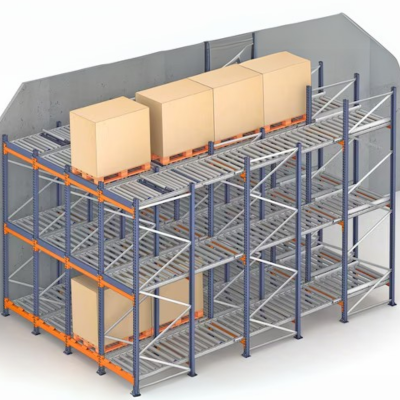
Pallet Flow Racking (Flow-Through)
This is a gravity-driven system perfect for FIFO inventory. Pallets are loaded from the back and flow forward for picking, reducing handling time and improving rotation.
Ideal for:
- Perishable inventory
- Fast-moving goods
- Warehouses needing storage solutions with high pick efficiency
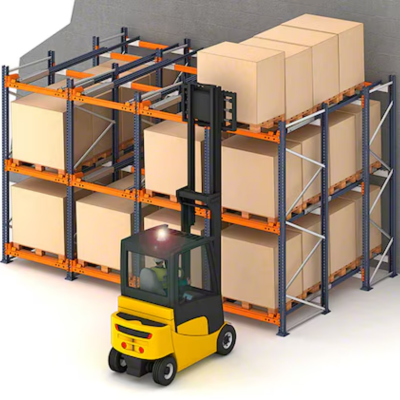
Push-Back Racking
This system uses inclined rails and carts to store pallets several deep, allowing pallets to roll forward when one is removed.
Advantages:
- Supports LIFO inventory
- Reduces aisle requirements
- Ideal for medium-turnover products
Push-back racking is an excellent choice for maximising both floor and vertical space in warehouses.
Cantilever Racking and Other Configurations
We also supply solutions for non-standard loads, such as industrial shelving for odd-shaped goods or cantilever racking for long items like timber or piping.
Our team of industry professionals can help identify the right system from our range of pallet racking options.
How to Choose the Right Warehouse Pallet Storage Racks
Selecting a racking system involves more than just knowing how many pallets you handle. Consider:
- The different types of pallet sizes and weights
- Your picking and replenishment frequency
- Available warehouse space
- Compliance with the Australian Standard AS4084
- Budget for installation and future expansion
As an established supplier of high-quality racking systems across South Wales and beyond, uTenant is ready to support your operational goals.
Why Partner with uTenant?
We're not just a supplier—we're your warehousing solutions partner. We offer a tailored approach to racking system selection, ensuring the result aligns with your operational strategy and long-term needs. Whether you're fitting out a new site or upgrading an existing one, we make it easy.
We also help businesses stock an extensive range of warehouse pallet storage racks and pallet racking and accessories through our national network of suppliers.
As Australia's established supplier, we ensure your system meets code, is installed safely, and integrates seamlessly into your broader logistics operation.
Storage Solutions That Grow With You
From various types of racking systems to types and configurations customised to your business model, we ensure you’re never stuck with the same product that doesn’t evolve with your needs.
Ready to find the perfect fit? Our team works with you to understand your throughput, space availability, and future goals, delivering a complete solution that scales.
Ready to Optimise Your Warehouse?
Whether you're opening a new facility or upgrading your existing setup, uTenant is here to help. We connect you with high-quality pallet racking systems that meet Australian standards and support efficient, safe warehouse operations.
Need an efficient way to find a 3PL provider to service your logistics requirements, submit your request on our PalletMatch platform and we'll do all the work for you.
If you’re looking for warehouse optimisation advice and racking solutions, contact our solutions team today.
* Sourced from Dexion - Industrial Storage