12 ways the coronavirus changed warehousing
The Coronavirus crisis placed unprecedented stress on supply chains, globally. Whilst most of the attention was focused on the transport industry and the difficulties it faced in moving goods around the world and even across State borders in Australia, the warehouse sector also experienced enormous challenges.
One of the major features of the Coronavirus crisis was the impact of erratic consumer behaviour on demand for goods, causing unpredictability on supply chains and an increase in volatility. Some product lines saw extraordinary demand, whilst the collapse in demand for many ‘non-essential’ items led to previously ordered and shipped cargo piling up at many warehouses, ports and airports around the world. The warehouse capacity problem got so critical, that according to some sources there was only a few weeks spare warehousing capacity left in some markets.
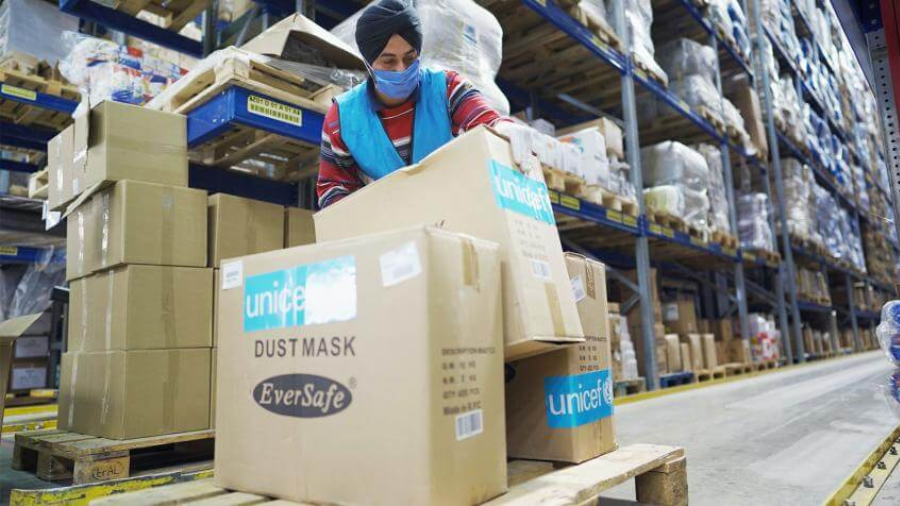
The problems were exacerbated by the phases in which the Coronavirus took hold in different locations. Demand for many Chinese made products in the West was still strong when the country exited lockdown in February/March 2020. This led to a wave of products being shipped arriving a few weeks later just as demand in Europe and North America collapsed. In many cases, this has led to a huge surplus of inventory being held in warehouses, awaiting an upturn in consumer and business demand.
There was no doubt that once lockdowns were in lifted in 2020, renewed economic activity would lead to some of these backlogs being drawn down, resulting in a surge in transport demand as goods moved to end markets. We predicted this would be followed by short term over-capacity in warehouses from a hiatus in replenishment due to many orders having already been cancelled with Asian suppliers. However, the impact of Coronavirus on warehousing was far from transient, and as we know, the effects lasted long into 2023.
Our insights and predictions from 2020
We originally published this article in June 2020, the very early days in what we now know was a longer than expected global crisis. Now that the Coronavirus crisis and global pandemic is over, we've updated this paper to be a retrospective on the insights and predictions that were published back in June 2020. This paper covers the long lasting consequences of the pandemic and how it accelerated a structural transformation in the way businesses deal with inventory.
Many companies and executives changed their view that ‘inventory is fundamentally evil’ (as espoused by Tim Cook, Apple’s CEO) to a far more nuanced analysis of its attributes – positive and negative. After all, holding inventory has proven to be a critical tool in a supply chain managers’ strategy in keeping customers supplied during times of social and economic disruption. Just look at the success the ‘high days of inventory on hand’ pharmaceutical sector has had in maintaining supplies of medicines to consumers and contrast that with the problems experienced in sourcing Personal Protective Equipment (PPE).
Nobody is suggesting a return to Just-in-Case (JIC) manufacturing or inventory management, or building up large stocks of goods which could rapidly become redundant. Such a policy would mean commercial suicide in many sectors not least due to the compression of modern product life cycles. Nor is such a ‘blunt’ approach necessary. To a degree, the need for inventory is created by the uncertainty caused by imperfect supply chain and market knowledge. Visibility systems play a fundamental role in addressing this void, allowing supply chains to become more agile – replacing inventory with visibility and the ability to make informed decisions.
This paper highlights twelve ways in which the warehousing sector was about to undergo a huge transformation. Some of these changes were driven specifically by Coronavirus; others were trends that pre-existed the pandemic but which were accelerated by the social and economics changes which it wrought.
1. LEAN to HIGHER INVENTORY
The first major trend – possibly the defining trend of the entire crisis – is that of increased inventory holdings. Warehouses are nodes in the supply chain where inventory builds up as an insurance policy against unforeseen peaks and troughs in demand. The more uncertain the market or the external environment, the greater the need for warehouses in which to store goods and the services required to process, pick, pack and dispatch them. In the future there will be less LEAN and more safety stock. Of course, an economic downturn will mean fewer volumes overall in the short term, but the metric of inventory to economic activity will rise.
The increased levels of inventory will need more warehouse capacity in which to store them. This additional capacity may come from larger warehouses, from more warehouses, or both. This will depend on individual industry sectors and the inter-relation of many of the dynamics addressed below.
2. IN-HOUSE to THIRD PARTY LOGISTICS
Following the crisis, manufacturers and retailers will be more likely to regard large numbers of warehousing staff on their payroll as a risk as much as an asset, especially with the ever present possibility that Coronavirus (or another global pandemic) may return at some point. Many may be tempted to believe that this is a challenge that would be better for a third party logistics (3PL) provider to deal with. One of the key strengths of 3PL providers is their ability to manage large work forces and these challenges will only increase in the coming years from a health and safety perspective.
3PL providers also often have existing networks of facilities in multiple geographic locations. As detailed below, it may be that downstream distribution requirements start to fragment, with the growing importance of local and urban markets as well as the increase in protectionism. If this is the case manufacturers and retailers will not necessarily want to build their own networks of distribution facilities required to meet the needs of these markets, instead relying on logistics providers to do this for them.

3. DEDICATED to MULTI-USER WAREHOUSE
Market turbulence is a strong challenge to dedicated, long-term warehouse operations which, to a large degree, works best in times of stability and predictability of demand. This may mean that there will be a move from dedicated (single-client) warehouses to multi-user (multi-client) warehouses. The new market environment will require greater levels of flexibility which allow manufacturers and retailers to ‘plug’ into existing warehousing operations. Short set up times, quick training of staff and off-the-shelf technology will be essential to allow customers to move into new markets as and when demand occurs. The growing requirement to serve smaller localised markets will also favour operations within existing distribution centres.
4. LONG-TERM to SHORT-TERM LOGISTICS CONTRACTS
Fourthly, there will be a shift from long-term to short-term contract lengths. One of the challenges of a highly volatile market is that warehouse capacity is often secured by manufacturers and retailers on a medium-term basis (3-5 years); some contracts are longer – up to 10 years. This may be satisfactory in a stable economy, especially in sectors such as consumer goods, where demand year-on-year for logistics services is consistent. However, if the market ‘new normal’ is wild variability then such a model will leave companies exposed to the risk of having too much (or too little) inventory as well as warehousing capacity located in the wrong markets.
5. GROWTH OF ON-DEMAND WAREHOUSING
As a follow up to this trend, for a niche part of the warehousing industry Coronavirus has presented opportunities – the so-called ‘on-demand’ sector including startup companies such as uTenant, FLEXE, Cubework, Stord, Stowga, W2G and Flowspace. The huge demand created for warehousing in some sectors by Coronavirus has led to more manufacturers, retailers and 3PL providers making more use of short-term and flexible warehousing capacity.
The business models of these companies varies. Some, like uTenant & FLEXE, offering a pay-as-you-go service, and others offering co-warehousing spaces. However, they all offer an alternative to the long-term lease or contract options, which take time to negotiate and lock the warehouse tenant into a solution which might become out-of-date almost immediately, in these days of volatility and uncertainty. Another part of these companies’ offering is the technology infrastructure which allows for ‘virtual’ warehousing. That is, allowing the visibility to store inventory in multiple locations across a wider warehousing network.

6. LOW INVENTORY to AVAILABILITY OF PRODUCT
Like many of the trends outlined in this paper, the growing priority for availability of product (as opposed to the minimisation of inventory) has not been caused by Coronavirus, but it was accelerated by it.
Amazon and other online retailing platforms have created a consumer ‘need’ for immediate, or near-immediate fulfilment of their orders. This change in consumer behaviour is not confined to the e-retail sector – it is influencing all of retail. The best example of this is in the US, where Walmart is focused on matching Amazon’s ability to deliver very quickly to the end consumer. This has pushed up its inventory holdings as it increasingly holds stock in multiple locations, close to the end market. Whilst allowing the company to deliver on a very short timescale, this does mean that inventory levels have felt an upward pressure.
The Coronavirus lockdown of consumers has driven up e-commerce volumes (although not necessarily profits, as in the case of Amazon) and engrained customer expectations of the level of service. Many believe that this will now become the ‘norm’. If retailers are to match the service provided by e-retail platforms, they too will need to devise strategies that either increase the level of stock in store from which to make home deliveries, or develop a network of smaller, more local facilities.
7. INCREASE IN SPECIFIC E-COMMERCE/OMNI-CHANNEL FACILITIES
As mentioned above, Coronavirus has helped to accelerate e-commerce sales. The requirements of e-commerce warehousing are quite different from those facilities serving grocery retailing, High Street shops or Department Stores. They must be designed for the fast flow of small, individual items often delivered by a variety of trucks and vans to the end-user. This is in contrast to the more infrequent delivery of consolidated items to a single store by truck and trailer. This means that warehouses are getting bigger as more room is required for the physical handling of so many smaller packages. Also, e-retail warehouse facilities are often open around the clock, picking and packing order shipments for next day delivery.
Whilst the e-commerce model requires warehouses with larger footprints, it will also be the case that there will be more e-commerce warehouses. Whilst some service levels – such as next day delivery - can be provided through the efficiency of transport networks from more centralised distribution facilities, same-day or quicker deliveries need hyperlocal fulfilment centres. This will require many more satellite warehouses from which shipments of a limited number of SKUs can be dispatched on an on-demand basis.
8. GLOBAL/REGIONAL to NATIONAL/LOCAL
Many supply chains involve the flow of containers from remote manufacturers based in Asia through ports in Europe or North America and on to distribution centres, from where the goods are distributed to other manufacturers or retailers. This entire process has come under scrutiny as various parts of the supply chain and the logistics which underpins it failed at times over the Coronavirus pandemic.
This has led politicians to call for the re-shoring of the production of essential goods (such as PPE and medicines). This argument has also been extended to the introduction of much broader industrial strategies which would promote the development of national supply chains. Hand-in-glove with this policy is protectionism. Relations between the world’s largest trading partners are as bad as they have been for many decades. US and China are in the midst of a protracted trade dispute and other major exporters to the US, such as Germany, will not be immune from ratcheting up trade tensions.
What is the impact of this on warehousing? Logically this should mean that there will be a migration of warehousing away from major shipping gateways to locations which are geographically more central and nationally based. Brexit in the UK, saw similar results, as supply chain managers became wary of the risks involved in bringing goods through bottlenecks, such as the Port of Dover, from the EU. In the US, there will be a re-balancing of volumes away from West Coast ports in particular.
Of course, this will be a gradual process. Much of Europe’s and North America’s manufacturing capacity has been lost over the last two decades and before. Consequently any repatriation of industrial production is likely to occur slowly.
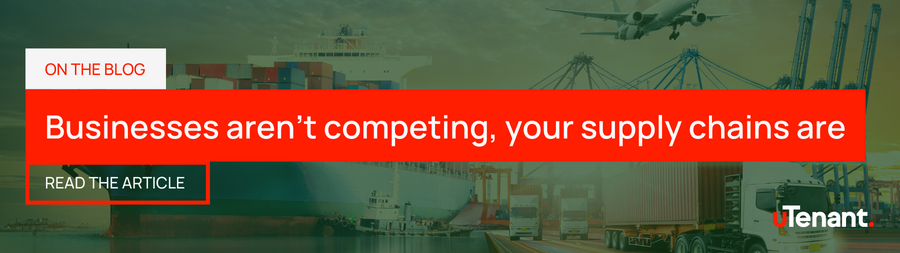
9. CENTRALISED to FRAGMENTED
Centralisation of warehousing has many benefits, not least the reduction of the overall inventory requirement within a supply chain by reducing levels of safety (buffer) stock required in individual distribution centres. However, by consolidating stock in a single (or at least fewer) warehouses, levels of external risk increase. These risks include:
> Fire or flooding
> Industrial action
> Natural disaster
> Disruption of transport and, of course,
> Pandemics
The latter had a major impact on many warehouse operations throughout the world. The industry is highly labour intensive and therefore susceptible to an outbreak of disease, especially in crowded warehouses. The reaction of warehouse operators has been to segment workforces and keep shifts separate as well as a host of other hygiene initiatives. However, as a response to Coronavirus, many may prefer to migrate to a greater number of smaller warehouse operations where outbreaks of disease can be contained and limit the impact of the spread of contagion on entire operations within the supply chain node.
10. MARKET-WIDE to CITY-FOCUSED
The significant drop in both Carbon Dioxide (CO2) emissions and those that effect human health (Nitric oxide (NO) and particulates) during the Coronavirus crisis, will double-down efforts by campaigners to maintain much lower levels of pollution. This will encourage governments to move forward with diesel bans in urban areas, in effect erecting a barrier to the distribution of goods to urban markets direct from a regional or national-based logistics facility. To meet this dynamic, distribution networks will have to become more complex and multi-layered. National distribution centres will likely serve Urban Consolidation Centres (UCCs) at the edge of urban areas. Goods will then be transhipped for delivery to logistics facilities located in the metropolitan area or delivered direct to consumers, in both cases, on alternative fuel powered vehicles. Logistics facilities in urban areas will necessarily be smaller due to higher rent costs and often located in residential areas, limiting access.
11. INCREASING AUTOMATION
The threat of Coronavirus – or for that matter, any disease – encouraged warehouse operators to increase levels of automation within their operations. Once again this is not a new trend, but one which was accelerated by the crisis. The low cost of borrowing money and government incentives for capital purchases will make the return on investment case attractive. Running contrary to this, in the short-term, unemployment levels and the migration of workers from the high street retail sector to logistics will make labour abundant and cheap. However, in the long-term the sector’s adoption of automated materials handling equipment and robotics is inevitable.
This will have implications for the design and types of warehouses that are constructed in the future. Few are up to the modern standard required for autonomous vehicles to move products around the facility (for instance, uneven flooring) and so there will have to be considerable new investment in the building stock.
12. MORE GREEN WAREHOUSING
Following the Coronavirus crisis, there will be renewed focus on sustainability, as mentioned above. The drop in carbon emissions during ‘lockdowns’ will encourage environmental lobby groups and governments to put in place policies which prevent (or at least slow) pollution levels from returning to their previous highs. Then in 2022, the Australian Government finally legislated Australia's greenhouse gas emission reduction targets. The National plan is to reach Net Zero by 2050, and by 2030 aim to reach emission levels of 43% below 2005 levels.
These environmental policies not just be aimed at the transport element of logistics (having implications for supply chains and hence the location and type of warehousing as detailed above in point 10) but warehousing will also be expected to contribute to the reduction in emissions. This will mean that new buildings will have to conform with increasingly prescriptive energy standards, Greenstar ratings, and environmentally friendly practices.
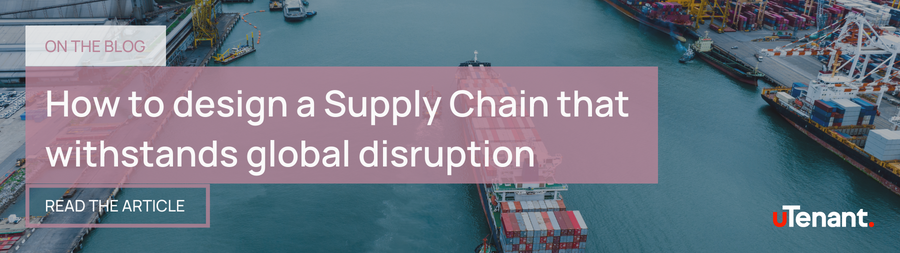
Conclusion
Coronavirus led to many of the key supply chain trends of the past three decades being challenged. It certainly won’t result in a compete upheaval of industry mantras, such as its just-in-time inventory model (focus on holding low inventory), but it will mean that companies take a far more nuanced or multi-faceted approach. Inventory has not suddenly become ‘good’. The more inventory held the greater the risk from redundancy, shrinkage and theft. In addition, the more cashflow tied up in inventory, the less can be invested in new product development or automation, for instance.
Technology supporters will no doubt maintain that visibility across the supply chain will play a crucial role in allowing inventory levels in warehouse storage to be constrained, whilst ensuring customers’ demands for ‘instant’ fulfilment are met, especially in the e-commerce sector. However, it is likely that this is only part of the solution. Inventory levels will inevitably rise as a response to the existential threat posed by supply chain risk, as laid bare by the Coronavirus crisis.
At the same time, it is likely that manufacturers and retailers will review the function of warehousing within their businesses. If they decide that employing workforces (which can often run into many thousands of staff) is just too much a risk, then 3PL providers will receive a boost from out-sourcing. They will also want to leverage 3PL providers' existing networks and benefit from the flexibility which they can provide. On the other hand, contract lengths may be pushed down, as clients become wary of the risk posed by being locked into a solution which may rapidly go out of date. At the extreme end of the spectrum, on-demand warehouse providers will benefit.
In addition to this, investment in automation will increase as warehouse companies of all types use cheap money to improve the resilience and efficiency of their operations. This will require substantial investment not only in the robotics and materials handling equipment but also in modern warehousing property stock. The development of modern warehouses to meet these new needs will also mean that buildings (and the processes within them) become more sustainable.
Original paper published by Prof John Manners-Bell, Chief Executive of Ti, Honorary Visiting Professor at the London Metropolitan University’s Guildhall Faculty of Business and Law and an adviser to the World Economic Forum.
uTenant has updated the above article to be a retrospective of the original paper, published in 2020, with some of our own commentary interspersed throughout.
Updated: 28 February 2024