5 top tips for leasing a warehouse: A guide for logistics operations
Leasing a warehouse is an important decision for third-party logistics providers (3PLs) or any type of manufacturing or product business that manages their own warehousing and distribution. Leasing a warehouse or industrial property requires serious consideration - from air conditioning to loading docks and power requirements, there are several factors to consider before you sign on the dotted line.
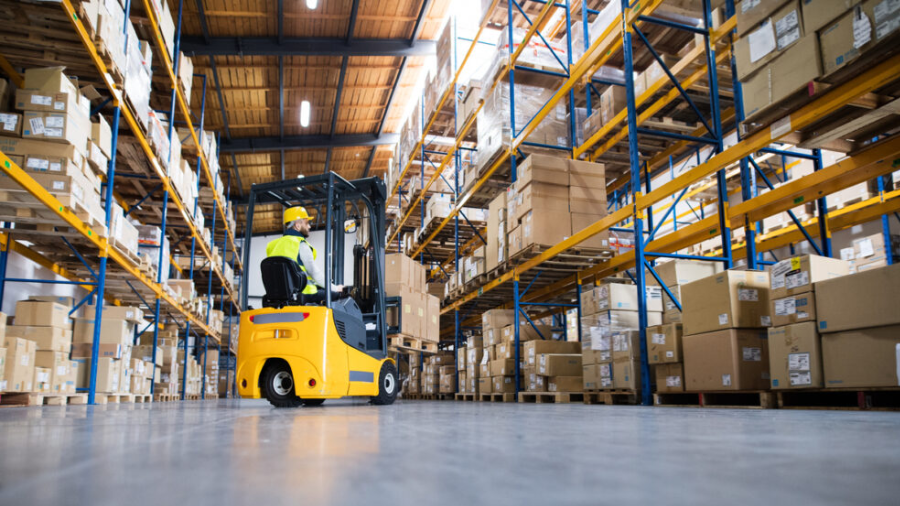
Ensuring your chosen industrial property meets your operational needs can streamline logistics and improve efficiency. Here, we outline five key considerations when leasing a warehouse for your logistics operations.
Evaluate your electricity or power needs when leasing a warehouse
Consider the electrical load and power requirements of your business when you inspect the building. It is critical to know if the warehouse is properly wired to suit your power needs. If the wiring at the warehouse or industrial space does not suit your requirements, in most cases you, as the tenant, will be required to pay to alter the wiring to suit your needs. For example, if you are running large electrical units such as air conditioning or any manufacturing equipment, your power requirements will be high and you will therefore require three-phase power to the building.
If you’re not sure if the warehouse or industrial space has what you require, it is recommended you hire the services of a professional electrician to fully inspect the building for you. It is best to get a complete electrical assessment before signing a lease for any industrial space or warehouse. This will ensure that the building includes the wiring and power capacity that you require to operate your business on the site.
Electricity requirements vary significantly based on your own warehouse activities, so before signing a lease, consider:
- Power capacity: Make sure the warehouse has adequate electrical infrastructure for your operations, especially if you use machinery or automation.
- Backup power options: For businesses that need continuous operation, check if the property supports generators or alternative power sources.
- Energy efficiency: Look for energy-saving features that can help lower operating costs, such as LED lighting and energy-efficient HVAC systems.
Understanding your power needs ensures you lease a warehouse that supports your logistics operation without unexpected power limitations.
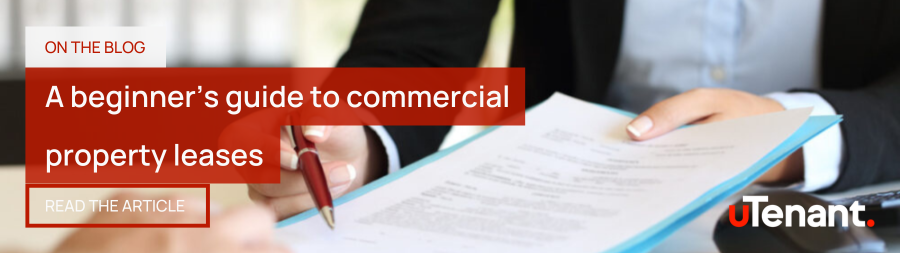
Assess your floor load requirements when leasing a warehouse
In warehouses and logistics facilities the concrete slab and flooring are critical to the effective functioning of the operations. Floor load is the load (weight) that a floor of the building can safely support, and is made up of static loads and dynamic loads:
- Static loads include for example, block stacking, equipment and machinery and storage racking systems.
- Dynamic loadings include material handling equipment (“MHE”), and other traffic including forklifts, pallet stackers and other vehicles.
If your business is installing heavy manufacturing equipment, it is especially crucial you consider the floor load capacity of the concrete slab against your intended use of the space. Some industrial machinery will require a minimum slab thickness to be capable of safely supporting large loads without cracking. If you will be installing or using heavy equipment inside the building (for example high capacity forklifts), first ensure that the concrete slab meets your exact weight and floor load requirements. Key aspects to review include:
- Weight limits: Verify the floor load capacity suits your inventory, especially if you store heavy goods or use equipment like forklifts.
- Floor condition: Inspect the floor for cracks, uneven surfaces, or other issues that could affect the safety and efficiency of your operations.
- Special flooring needs: If your logistics operations require specialized flooring, such as anti-slip surfaces or reinforced concrete, ensure the property can accommodate these.
The warehouse floor's load-bearing capacity is essential for supporting your storage (inventory) and equipment.
Ensure the warehouse has adequate loading areas
Logistics efficiency depends on having well-designed loading and unloading areas. Loading areas/delivery docks are important for safe building access and efficient operations, and are often overlooked when leasing a warehouse space.
For example, do you require a warehouse space that will be receiving or dispatching goods from large or long vehicles? Large or long vehicles require extra space to safely maneuver around the building, and many older industrial properties may not be able to accommodate this requirement. Before leasing a warehouse you should also do your research on the local road network that will be used to access the warehouse to ensure roads are compliant with the types of vehicles you will be using.
When leasing a warehouse, consider:
- Number of loading docks: Ensure there are enough docks to handle the volume of inbound and outbound shipments without bottlenecks.
- Dock height and equipment compatibility: Check that the loading dock height and configurations match the types of vehicles used in your logistics.
- Traffic flow: Evaluate the layout to ensure smooth movement of vehicles and personnel around the loading areas, minimising delays.
Consider your operational requirements and allow plenty of access for those goods.

Heating, ventilation and air-conditioning (HVAC) considerations for your warehouse
When leasing a warehouse or industrial space it is important to consider the heating, ventilation and air-conditioning (HVAC) requirements of your operation. If the HVAC system in the space is too small or doesn’t have sufficient units it may create an unhealthy working environment. If it is too big, it could cost you more to operate it than you planned for.
Heating, ventilation, and air conditioning play a vital role in maintaining the ideal environment for different types of inventory. Consider:
- Temperature control requirements: If you store temperature-sensitive goods, ensure the warehouse has adequate HVAC capabilities for cooling, heating, or humidity control.
- Energy costs: Factor in the cost of running HVAC systems, especially if you operate in a region with extreme weather conditions.
- HVAC maintenance responsibilities: Clarify in the lease agreement whether the landlord or tenant is responsible for maintaining HVAC systems.
If the building HVAC system appears to be adequate, it is still advisable to have the system inspected by a certified HVAC technician to ensure that it is in good working condition before signing the warehouse lease.
When negotiating your lease it is recommended you include HVAC maintenance and servicing as a maintenance cost that you are responsible for and any major repairs or replacement as the landlord’s responsibility. If either the heating, ventilation or air-conditioning does not suit your company’s requirements, it is very likely that you, as the tenant, will be responsible for the cost of any changes.
Are property changes allowed when leasing a warehouse?
When leasing a warehouse it's important to remember that your operations may require specific modifications to the property. Normally, a commercial lease allows tenants to make modifications or improvements to the property, but there will likely be a make good clause which you have to accept.
Before committing, review:
- Permitted alterations: Understand what changes you can make to the warehouse, such as installing mezzanines, adding shelving, or modifying loading areas.
- Restoration requirements: Check if the lease agreement requires you to restore the property to its original condition upon lease termination.
- Landlord approval processes: Make sure you know the steps and timeframes for getting landlord approval for any alterations.
The lease agreement should also contain details of who is responsible for paying for any modifications or improvements required, such as electricity requirements, heating and/or air-conditioning or loading dock access. Ensure that the agreement also stipulates who owns the improvements at the end of the lease.

Ensure your chosen industrial property meets your operational needs before signing that warehouse lease
Leasing a warehouse is more than just finding a space to store goods; it's about securing a facility that aligns with your logistics strategy and supports your business growth. Remember these five tips:
- Understand your power needs to ensure you lease a warehouse that supports your logistics without unexpected power limitations.
- Matching the floor's capacity with your load requirement prevents damage and reduces risks associated with overloading, avoiding potentially costly mistakes.
- A properly set up loading area is crucial for maintaining logistics efficiency and reducing turnaround times for shipments.
- Proper HVAC management can prevent damage to goods and create a safer working environment for employees.
- Knowing the limitations on property modifications allows you to plan your warehouse setup effectively, and know which property is the right one for you to lease.
A well-chosen property and warehouse lease can significantly boost efficiency, reduce costs, and create a competitive advantage, empowering your business to thrive in an ever-evolving landscape. Make informed decisions now, and set your operation up for lasting success.
If you’re searching for an industrial space or warehouse, submit a requirement request with uTenant to find a suitable space quickly and efficiently. uTenant is simple to use, convenient and online - what could be easier?

Frequently asked questions (FAQs)
What should I consider when leasing a warehouse for logistics?
When leasing a warehouse, consider factors such as size, location, lease flexibility, and additional costs. Tailor these considerations to your specific logistics needs, such as seasonal storage or specialised handling requirements.
How does a commercial property lease work for industrial spaces?
A commercial property lease typically involves a rental agreement specifically for industrial properties, like warehouses. It may include base rent plus additional costs for maintenance, insurance, and utilities. Lease terms vary, so it's important to understand all the conditions before signing.
What is the difference between leasing and buying a warehouse?
There are benefits to both buying and leasing space, depending on your intention of use for the property. Leasing offers flexibility and lower upfront costs, making it ideal for businesses with fluctuating logistics needs. Buying a warehouse provides stability and potential equity growth but involves higher initial investment and maintenance responsibilities.
What should I consider regarding power needs when leasing a warehouse?
Evaluate the electrical infrastructure, backup power options, and energy efficiency to ensure the warehouse can support your operation.
Why is floor load capacity important in a warehouse lease?
The floor's load-bearing capacity is critical for safely storing inventory and using equipment. Verify that the property meets your requirements to avoid operational risks.
How does HVAC impact logistics operations in a warehouse?
HVAC systems help maintain optimal conditions for inventory and staff. Consider your temperature control needs and the associated energy costs.
Updated: 25 October 2024