The 6 KPI’s that will make or break your warehouse
Your warehouses are your cost centres, and a successfully operated warehouse can save your business a lot of money. Therefore consistent Key Performance Indicators (KPI’s) will allow you to optimise on your warehouse and inventory operations.
When I think of KPI’s, I think of the 20 calls a day I used to have to make back in my Sales days. Because 20 calls meant at least 5 quality conversations. And 5 quality conversations meant one warm lead.
KPI’s are vital in tracking, identifying and defining progress towards your business goals, and are essential to the success of any organisation.
I see a lot of businesses today use innovative ways to measure performance, especially in the warehouse and inventory space. With COVID-19 throwing a few unexpected challenges into the mix, your warehouse operations need to be working effectively and efficiently.
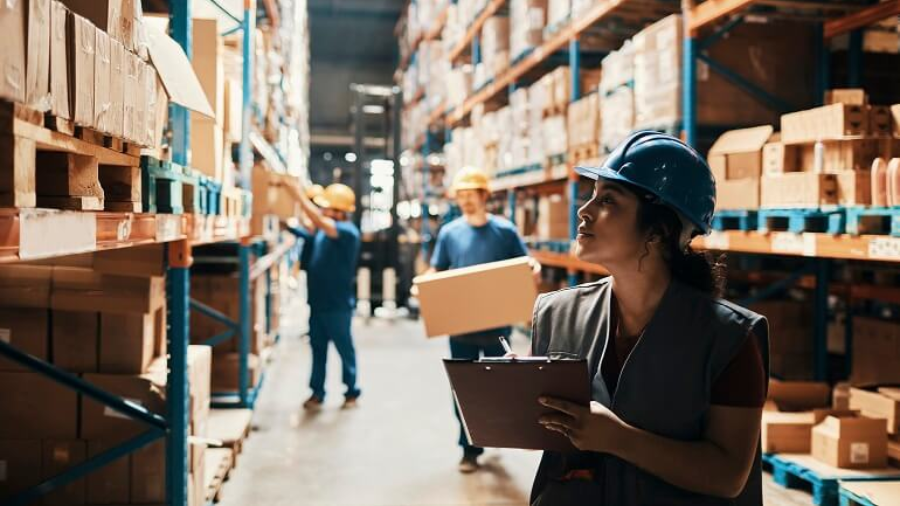
So without further ado, your 6 KPI’s you need to be tracking, that will help you succeed:
1.The speed of you inventory turnover
Sales ÷ Average Inventory or Cost of Goods Sold ÷ Average Inventory
Measuring the frequency at which you sell out your inventory is crucial to your business. With inventory holding a significant amount of funds, you need to know what is sold and what is not selling.
Not only does carrying inventory also cost you money, you cannot make money either. Slow-moving stock takes up valuable pallet space and significantly decreases warehouse efficiency.
2. The carrying cost of inventory metric
Carrying Costs ÷ Overall Inventory Costs
This is the cost of storing pallets and inventory over a certain timeframe. Unnecessary inventory taking up warehouse space means additional labour costs, risk and insurance costs as well as storage and freight fees.
Knowing how to track the cost of carrying inventory means you can identify how much profit your current inventory brings, and reduce obsolete, slow-moving or dead stock inventory.
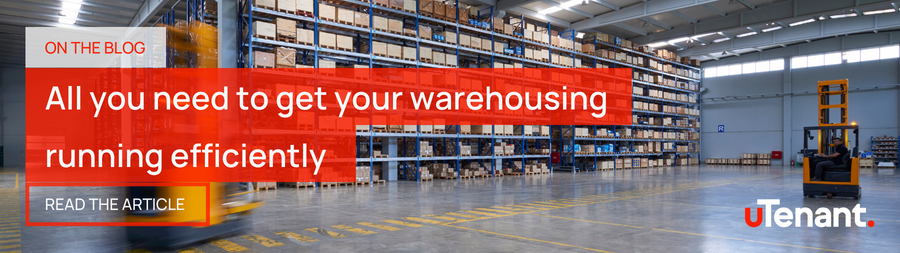
3. The efficiency of your receiving area
The time between point of delivery & items being ready for sale
Keeping tabs and recording timestamps on your receiving area is often ignored, as other parts of the warehouse take precedence. But anything from the space your staff need to how quickly inventory is counted, receiving deficiencies can have a domino effect to the rest of your warehouse operations.
4. Perhaps a more difficult KPI to monitor, but essential all the same - Put-Away
Factors to consider when measuring your Put-Away KPI’s:
- Accuracy Rate
Inventory Put Away Correctly ÷ Total Inventory Put Away
- Cost per item put away
Total Cost of Put Away ÷ Total Line Items
- Man hours & time it takes from receiving to picking location
Total Time for Put Away ÷ Total Time
5. Rate of return
Rate of return = (Units returned ÷ Units sold) x 100
Tracking your rate of returns is a simple yet essential warehouse management KPI, but the key to optimising this KPI is segmenting the returns by reason.
6. Warehouse Safety KPI’s
Number of days since the last accident
Lost Time in Hours Due to Accidents ÷ Total Number of Hours Worked
Ideally, you want zero accidents a year, but this is unrealistic and accidents are just that - accidents. Unintentional. However, high accident rates a year could signal larger issues in workplace safety.
Keep aiming for a high number of days since the last accident and use these KPI’s as a good benchmark to how safety training and follow through is working.
It is essential to track KPI’s in your warehouse operations. They are directly related to the overall efficiency of your supply chain as well as the quality of your customer service, and your demand of inventory.
Published: 2 September 2020