The truth behind AGV’s
How they could help or hinder your warehouse efficiency
Love it or hate it, the rise of automation in warehousing and logistics feels inevitable. As the market becomes increasingly competitive, reducing overheads while increasing efficiency is the holy grail of logistics; and that’s where automation can really shine.
But fully automating a warehouse is a huge commitment, requiring a large financial investment, lots of downtime while the conversion occurs, and a quantum shift in how things are managed. For those businesses not ready to make the leap to full automation, Automated Guided Vehicles (AGVs) can offer many of the same benefits for a fraction of the investment…or do they?
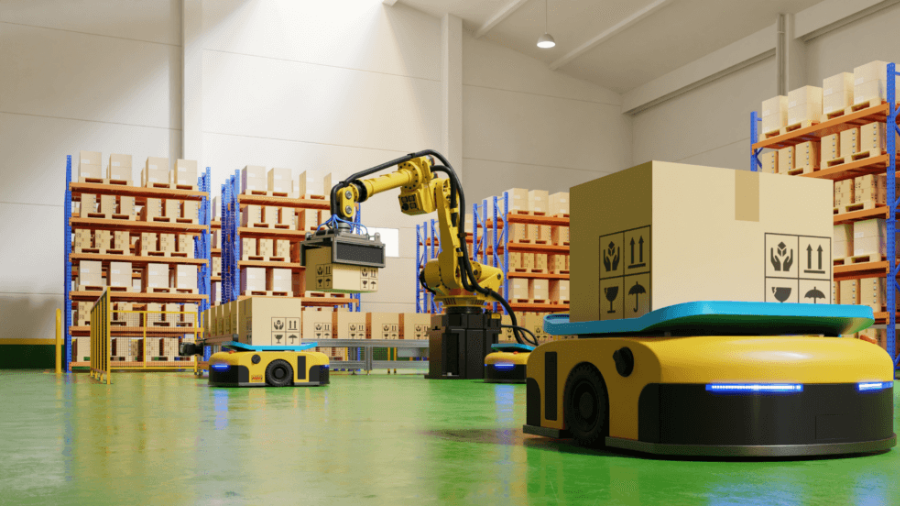
What are AGVs?
Automated Guided Vehicles are vehicles that function without a human operator. While AGVs are used in many applications across an increasing number of industries, warehousing is one of the most common.
These autonomous, driverless vehicles come in a wide array of sizes and shapes, all created with a specific purpose in mind. From Very Narrow Aisle trucks that can operate in tight spaces, to heavy load carrier capable of moving even the largest items, there’s an AGV for almost every warehousing application.
The benefits of AGVs in your warehouse
There’s a reason more and more businesses are utilising AGVs in their warehouses – particularly as their price comes down and their functionality increases. Here are some of the key reasons a number of our warehousing clients have embraced AGVs…
Productivity
In the quest for efficiency, AGVs are a powerful tool. While not always as fast as manned vehicles, AGVs have the ability to work longer hours - around the clock if needed – with less downtime, which more than makes up for their lack of outright speed. When integrated with a Warehouse Management System (WMS), AGVs allow for accurate and up-to-the-minute inventory management, a cornerstone of an efficient warehouse.
No Mistakes
One of the leading causes of unplanned downtown is human error. By removing the human, AGVs also remove those costly errors, saving time, money, and improving inventory management. When compared to manned vehicles, AGVs are also much safer, thanks to the cutting-edge sensors they’re loaded with. This allows them to operate in close proximity to other personnel with much less risk involved than traditional warehouse vehicles.
Reduced overheads
While AGVs aren’t cheap (although that’s beginning to change), they have very few ongoing costs once that initial investment has been made. Unlike employees, you don’t need to pay an AGV wages, healthcare, insurance, or paid leave and while there are ongoing maintenance costs, these pale in comparison to staffing expenses. With labour accounting for up to 70% of a business’s total costs, AGVs can be a fantastic way to reduce overheads without sacrificing on productivity.
No infection risk
A year ago, this probably wouldn’t have been a factor on many people’s lists, but the COVID-19 pandemic has highlighted how vulnerable warehouses are to disruption. Unlike people, AGVs don’t transmit disease, allowing them to operate uninterrupted throughout any outbreak. Recognising this, many hospitals used AGVs to transport PPE and other materials to where they were needed throughout the pandemic. This not only avoided any potential cross-contamination but also freed up valuable resources that could then be allocated to other areas.
The Downsides of AGVs
Despite their many positives, AGVs aren’t a perfect fit for every business. In some cases, they may not be able to deliver the benefits and may even hurt the efficiency of your warehouse. Here are some of the potential downsides of AGVs that you should be aware of…
Rigidity
AGVs ability to perform a specific task is one of their strongest points, but it can also be a weakness. Many AGVs are one trick ponies, capable of doing a single job accurately, reliably, and efficiently…and not much else. While certain models can carry out multiple tasks or allow for modular attachments, they don’t have the flexibility or ability to think creatively and solve problems that a human does…for now!
The cost
While generally cheaper in the long run than an employee, the significant upfront cost of AGVs can make them unfeasible for some businesses. In addition to the price of the vehicle itself, some workspaces may also need to be modified to allow it to operate effectively. From moving storage racks to clear a path, to levelling uneven surfaces or installing new power systems, there could be hidden costs involved in getting your warehouse “AGV-ready”.
Walled garden
Sitting behind every AGV is a management system, which allows the vehicle to be programmed and monitored. While some AGV management systems are universal, many are specific to a certain manufacturer, and these proprietary systems don’t communicate with each other. This can lead to businesses being limited to a single manufacturer or having to invest heavily in the infrastructure that can allow them to use AGVs from multiple brands.
Are AGVs right for me?
Before deciding whether to invest in an AGV, there are some fundamental questions to ask yourself. Are your labour costs high enough to justify the initial purchase price? Do you have repetitive tasks that would be suited to an AGV or is being agile and more important? While automation can be a great way to increase efficiency, that’s not always the case – so think about your specific situation and goals before taking the plunge.
Fortunately, unlike converting your warehouse to full automation, AGVs can be introduced slowly and with comparatively minimal investment. If you think your operation would benefit from autonomous vehicles, you can purchase one or two that will deliver the best return on investment and the scale up your AGV fleet if you get the results you’re looking for.
uTenant know warehousing, and we know how to create systems that make your operations efficient and effective. Our supply chain solutions team can help you review and improve your operations.
Published: 24 March 2021