What COVID has taught us about the value of flexible warehouse & 3PL models
Creating smart and nimble supply chains is the key to building a global trade and investment network that’s capable of weathering future storms. COVID-19 has revealed the fragility of the modern supply chain and warehousing structure. But humans have an innate ability to learn from experience and bounce back after destructive events. While the COVID-19 pandemic is far from over, now is the time to take stock of what needs to change to enable the creation of more efficient and resilient supply chains. By carefully observing where virus-related factors have caused problems and disruptions, and taking steps to address them, the global exchange of goods on which we all rely can become much more durable.
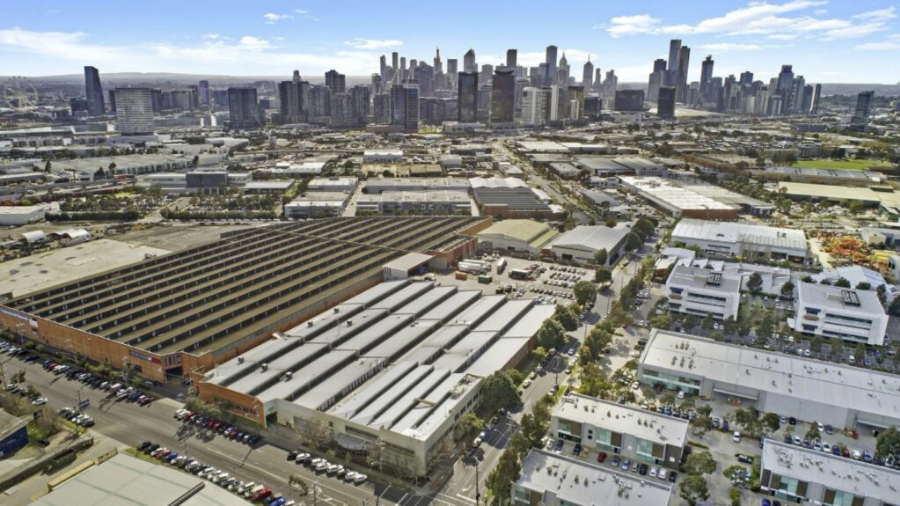
We are moving from just in time inventory model to a “just in case” model. Furthermore, e-commerce was already proliferating as we know, but some say COVID has expediated our online demand by 5 years. At uTenant, we can this the move from “Shop to Shed”. With stores closing and more people buying online, the stock has to be stored somewhere, right? Where? The Warehouse or what others call an Industrial Property (Real estate industry vernacular)
Since COVID, the supply chain has become the main protagonist for each organisation. We have seen a shift from a “behind the scenes” business role to one that is the prime driver of operational success.
Why?
COVID-19 has revealed the weaknesses of many parts of the supply chain. In order to respond to upcoming disruption and a continuing crisis, we need to fundamentally rethink supply chains and warehousing models. Remembering that we’re only as good as our weakest link…
Our goals in the medium term should be to modify the supply chain and the warehousing model as a key business driver and putting in a flexible asset as the most crucial factor for an agile business to succeed.
In the long-term, we need to look at the role of automation and AI to reduce risk and streamline operations. This was always the plan, but COVID has taught us to speed up implementation as technology and machine learning becomes more mainstream.
Automation was always in the pipeline for warehouses, but thanks to COVID (and the looming economic recession it brought with it), the speed in which companies are willing to implement smart technology into their warehouses has increased.
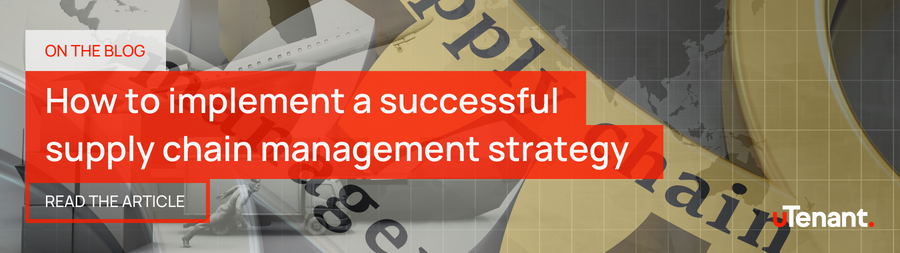
But in the meantime, we need a solution now. One which is cost-effective and time-efficient.
Here are three ways flexible warehousing models can help navigate your business through this pandemic:
1) Agile inventory solutions
As the term panic buying has become a well-known headline around the world, smart inventory management has been at the forefront of this solution. As companies have had to adjust their manufacturing capacity or shift their product margins entirely, organisations have needed to adapt quickly to create more flexible operating models. And as businesses needed to re-balance their inventory, more flexible storage solutions and partnerships became essential during short term volume peaks.
At the time of writing (on the day) Melbourne entered a state of disaster. And, by the time you are reading this article, will have made it extremely difficult for businesses with internal logistics and Third Party Logistics operators in Melbourne for instance. For example, companies with National Distribution Centres (NDC’s) here will struggle to fulfil customer orders nationally. We have had customers come through our platform scrambling to find warehousing solutions in other states for their fast-moving SKU’s so they can service their national clients.
If companies have all their eggs in one basked ie stock in Melbourne, they may decide to hold more products within a 3PL model in Sydney, Brisbane and Perth to ensure they can meet their customer’s fulfillment requirements. Therefore, we may see this trend continue in the months and years to come.
2) Assisting in efficient last-mile delivery
As the AU continues to flex its economic muscle, many companies are struggling to make long term distribution and real estate investments and partnerships. As retail giants like Amazon continue to increase their speed of fulfilment to either same or next day delivery, warehouse and distribution centres need to find a way to keep up with consumer demand, as online shopping habits continue to change. This will help businesses meet the need for speed - without escalating costs. Conventional warehousing typically involves multi-year contracts for an entire warehouse; however, as COVID continues to create uncertainty, this traditional warehouse model is becoming stagnant. We’ve heard these words a million times, flexibility and agility, but having this ability to adapt quickly is essential as the rampant shortage of warehouse space continues. As the rest of the supply chain adapts, warehousing space also needs to adapt.
I won't be surprised to see old retail stores that are closer to consumers repurposed as mini-warehouses or micro fulfilment centres. Retail bulky goods and underground carparks may follow this trend.
3) The option of a co-warehousing space
As demand continues to unpredictably and unexpectedly fluctuate, we can no longer rely on Big Data to prepare for the next wave of consumer expectation. Co-warehousing is a useful way to solve this problem. By filling unused warehouse space, we enable greater efficiency of labour, fill available space, boost revenue, and focus on short term flexible solutions. As we enter into a new phase of “normal”, the collaboration will be the centrepiece of business success, co-warehousing offers flexibility and solution to unpredictable demand.
By implementing the above three solutions, you remove the limits of non-flexible warehousing space and open your options to include a win-win scenario for both landlords and tenants, and all business parties. You have more control over the flexibility of your warehousing space and therefore, more control over the uncertainty of the current business climate. With better inventory planning, a more innovative and agile system, and a more flexible operations model, you will save cost, streamline processes and ensure the overall success of your business through COVID-19.
At uTenant, we’re the world’s first on-demand warehousing provider that doesn’t “broker” or “clip the ticket” on finding and filling space through our platform. We simply want to help tenants and landlords alike thrive through these volatile times and come out the other end with their recess and roller doors open for containers and tautliners alike. We believe we have a vital role to play in the industrial prop tech industry as we aim to become the world’s largest warehousing marketplace. To close, I want people to remember that in the perfect supply chain, a warehouse doesn’t exist, period.
For more information about how uTenant can assist with your flexible warehouse model contact us now.
Published: 14 August 2020