Effective warehouse picking strategies
Efficient warehouse picking strategies are the backbone of any streamlined supply chain. Whether you're managing a high-volume fulfilment centre or scaling up operations, choosing the right picking system can dramatically improve picking efficiency, reduce errors, and fulfil customer orders faster.
But what are the most effective warehouse picking strategies? And how do you know which one suits your operation best?
This guide breaks down industry-leading picking methods, enabling warehouse managers to select, implement, and optimise the right strategy for their team. From discrete picking to zone picking, we’ll explore how each approach fits into different warehouse operations, and how you can use cutting-edge technology to gain a competitive edge.
TL;DR
Choosing the right warehouse picking strategy is key to improving fulfilment speed, picking accuracy, and customer satisfaction. This guide breaks down common methods—discrete, batch, cluster, zone, and wave picking—and explains when to use each. It also covers how technologies like voice picking systems, pick-to-light, RFID, and warehouse management systems (WMS) can streamline operations. Whether you're scaling up or optimising an existing setup, aligning your strategy with your warehouse layout, order volume, and team capabilities is essential for success.
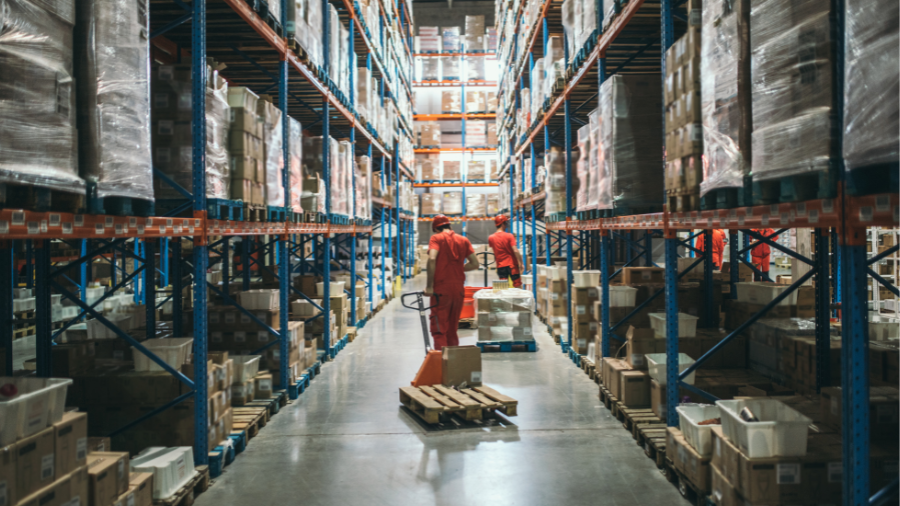
What Is Warehouse Picking?
Warehouse picking refers to the process of locating, selecting, and retrieving the correct items from storage locations to complete customer orders. This crucial function sits at the heart of the order picking process and significantly affects customer satisfaction, delivery speed, and overall warehouse performance.
Depending on your warehouse layout, SKU diversity, and order volume, different picking strategies may be required. A small warehouse with limited SKUs might benefit from discrete picking, while large warehouses with high-volume e-commerce activity may need more scalable options like cluster picking or wave picking.
Why Do Picking Strategies Matter?
Your chosen warehouse picking strategy directly influences not just how fast your team can pick, but also how accurate and cost-effective the process is. Poorly planned picking operations lead to incorrect items, long walks between warehouse shelves, and delays in the packing process — all of which erode customer satisfaction and inflate labour costs.
Key factors impacted by your picking strategy include:
- Picking routes: Efficient picking routes reduce time spent walking within the warehouse.
- Inventory management: Strong alignment between your picking process and inventory management reduces out-of-stocks and mispicks.
- Order accuracy: Picking errors hurt brand trust and increase return handling costs.
- Warehouse staff training: Clear, repeatable strategies help you onboard and train faster with fewer errors.
In short, your picking system must be tailored to your business needs and warehouse constraints — with a focus on maintaining high accuracy, fast fulfilment, and smooth coordination between order pickers, packers, and warehouse managers.
Core Types of Warehouse Picking Strategies
Here’s a breakdown of the most widely used and effective picking strategies, each designed to suit specific order picking needs:
1. Discrete Picking
Also called piece picking, this simple method has a warehouse worker pick one complete order at a time. It works well for operations with lower order volume, limited SKU variety, and straightforward fulfilment flows.
✅ Best for: Small warehouses, B2B orders
❌ Not ideal for: High throughput or complex warehouse order picking
2. Batch Picking
In batch picking, workers gather items for multiple orders simultaneously, which significantly reduces walking time. It’s ideal when you receive several orders containing the same SKUs.
✅ Best for: High-volume operations
❌ Not ideal for: Large, scattered SKU layouts
This method relies on barcode scanning and well-optimised picking routes to avoid confusion. When used with a warehouse management system, it can dramatically increase throughput.
3. Cluster Picking
Cluster picking takes batch picking further by grouping items into bins or totes based on the specific warehouse order. This reduces errors during the packing process and supports better picking accuracy.
✅ Best for: Multi-order environments
❌ Not ideal for: Warehouses without system support for real-time bin tracking
Proper labelling, shipping labels, and digital tracking help ensure picked items are sorted accurately for each destination.
4. Zone Picking
Zone picking divides the warehouse into areas where workers only pick within their assigned picking location. Once all zones have completed their portion of an order, items are merged before packing.
✅ Best for: Large warehouses with many SKUs
❌ Not ideal for: Small operations with centralised inventory
Zone picking improves picking efficiency and reduces bottlenecks. It’s highly effective when supported by a robust warehouse management system and automated radio frequency identification tools.
5. Wave Picking
With wave picking, your WMS releases orders in timed waves based on delivery schedules, order types, or SKU commonality. This structured approach helps manage labour and warehouse operations effectively.
✅ Best for: E-commerce or retail fulfilment
❌ Not ideal for: On-demand, unpredictable order flows
Wave picking is best paired with verbal instructions via voice picking tools or pick-to-light systems for added speed and real-time coordination.

Technology For Warehouse Picking
Modern warehouses rely on cutting-edge technology to boost speed, reduce errors, and improve the order picking process. Whether you're running a lean team or managing a complex fulfilment network, these tools can dramatically streamline your warehouse operations.
Voice Picking Systems
Voice picking systems are software and hardware solutions that enable this hands-free picking method. They integrate with your warehouse management system to provide real-time updates and validate picks as they happen.
- Improves safety and speed
- Reduces manual data entry
- Enhances worker movement and efficiency
- Integrates with WMS and inventory systems
By keeping workers’ hands and eyes free, voice picking supports efficient picking routes, especially in environments with high SKU complexity or rapid order fulfilment demands.
What Is a Voice Picker?
A voice picker is a warehouse worker who uses a voice-directed picking system to fulfil customer orders. Instead of relying on printed lists or handheld scanners, the picker receives verbal instructions through a headset. These commands guide them to the correct picking location, specify the item to retrieve, and confirm the pick.
This approach is designed to reduce manual processes, improve order picking speed, and increase overall picking accuracy.
Pick to Light Systems
Pick-to-light systems guide order pickers using visual signals—typically LED lights at picking locations. These systems are ideal for fast-moving warehouses where minimising time per pick is essential.
- Enhances picking accuracy
Easy to train new warehouse staff
Reduces reliance on paper or screens
Pick-to-light solutions are often paired with barcode scanning and integrated into broader warehouse management and inventory management systems.
Barcode Scanning & RFID
Barcode scanning remains a core element of most warehouse picking strategies. When enhanced with radio frequency identification (RFID), it offers live updates on inventory management, item locations, and picking accuracy.
RFID allows warehouses to monitor inventory levels in real time, eliminate misplaced items, and reduce delays. This is especially useful for multi-order picking, where items for multiple orders must be sorted quickly and precisely.
Warehouse Management Systems (WMS)
A powerful warehouse management system orchestrates every aspect of your picking and packing process—from inventory control to routing and labour allocation. A modern WMS supports:
- Batch, cluster, zone, and wave picking
- Order tracking with barcode scanning
- Integration with voice picking systems and pick-to-light systems
- Real-time stock levels and slotting optimisation
Investing in a scalable warehouse management platform reduces reliance on manual processes and gives warehouse managers greater visibility into performance metrics.
Robotic & Automated Picking
Automated systems—like autonomous mobile robots (AMRs) and robotic arms—are reshaping the future of warehouse picking. These automated processes reduce dependence on manual labor, especially in regions facing labor shortages.
Examples include:
- Collaborative robots that assist with repetitive tasks
- Automated sortation systems for high-volume fulfilment
- Voice picking paired with mobile robots for hybrid workflows
- Smart warehouse layout designs that support robotic efficiency
As these technologies evolve, they enable warehouses to meet higher demands, reduce operational costs, and maintain picking efficiency even during seasonal spikes.
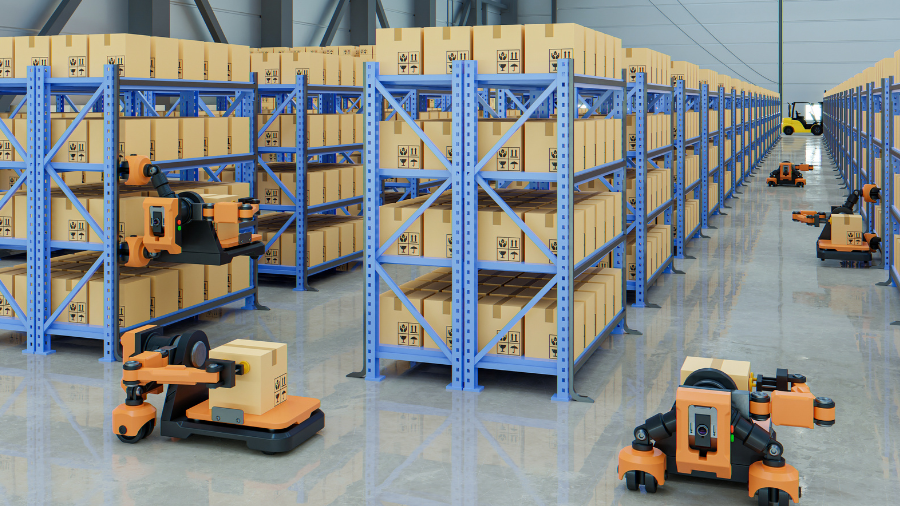
Best Practices for Warehouse Order Picking
To truly unlock the benefits of your chosen picking strategy, apply these best practices to your everyday warehouse operations:
1. Optimise Picking Routes
Whether using batch or cluster picking, optimise picking routes to reduce walking time within the warehouse. Group fast-moving items closer to the packing station, and regularly review layouts to maintain efficient picking routes.
2. Slotting for Accessibility
Place popular items in easily accessible locations and ensure SKUs that are frequently picked together are stored nearby. This boosts productivity across all picking methods, including zone picking and multi-order picking.
3. Use Standardised Packing Processes
Once picked, items should follow a streamlined packing process. That includes using the correct packing slip, verifying with barcode scanning, and printing accurate shipping labels.
4. Train Warehouse Staff Properly
Even with automation, human workers remain essential. Offer proper training on warehouse picking strategies, devices, and tools to avoid mispicks and delays. This is critical for scaling up safely.
5. Regularly Review Processes
Monitor your warehouse performance using KPIs like picking accuracy, order picking time, and error rates. Adjust strategies, invest in new tools, and ensure your team is aligned with fulfilment goals.
How to Choose the Right Warehouse Picking Strategy
There’s no one-size-fits-all approach when it comes to choosing the best warehouse picking strategy. The right method depends on your order volume, SKU diversity, warehouse layout, and the technologies at your disposal. Here’s how to approach your decision.
Evaluate Warehouse Order Types
Some strategies, like discrete picking and piece picking, suit low-volume operations where orders are simple and infrequent. Others—such as multi order picking, batch picking, and cluster picking—support more complex fulfilment centres where multiple orders must be filled at once.
Understanding your customer demand and peak periods helps in determining how to manage labour and technology effectively.
Review Warehouse Layout and Flow
In large or segmented warehouses, zone picking or pick and pass strategies offer significant gains in efficiency by reducing travel time between storage locations. Optimising warehouse shelves and picking locations for accessibility will support both manual and automated systems.
Assess Available Technology
If your facility is equipped with voice picking systems, pick to light systems, or integrated warehouse management systems, you can adopt more advanced methods like wave picking or automated sortation systems. These systems support efficient picking while improving order accuracy.
If you're not yet equipped, start with scalable tech like barcode scanning or radio frequency identification (RFID) to lay the foundation for digital transformation.
Consider Labour Resources
Evaluate your warehouse staff’s familiarity with technology and ability to adapt. Strategies like voice picking and collaborative robots can ease the load during high-demand periods and reduce reliance on manual labour.
Remember, consistent proper training ensures any strategy is implemented smoothly—whether your workforce is new or experienced.
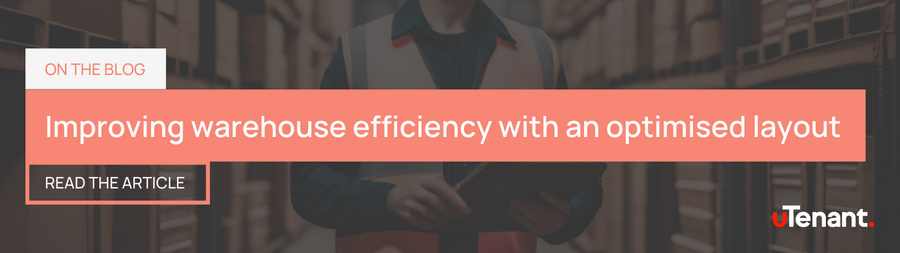
Why Packing Strategy Matters
Once items are picked, a well-defined packing strategy ensures accurate fulfilment and efficient delivery. The packing process has a direct impact on customer satisfaction, shipping costs, and operational efficiency.
Best practices include:
- Ensuring packing stations are fully stocked and well-organised
- Including accurate packing slips with every order
- Using shipping labels generated directly from your WMS
- Matching packaging to item size to reduce waste and save on freight
A streamlined picking and packing process helps ensure satisfied customers, fewer returns, and faster turnaround.
Optimise Warehouse Order Picking for Efficiency and Scale
Improving the picking process is one of the most impactful changes you can make to your warehouse. It boosts throughput, reduces labour costs, and improves customer satisfaction by ensuring orders are picked and shipped accurately.
Whether you’re managing warehouse processes manually or introducing advanced systems like automated sortation, voice picking, or collaborative robots, the key is to match your picking strategy to your unique business needs.
Keep your team trained, your tools optimised, and your data under review—because in a competitive market, efficient picking isn’t just a nice-to-have. It’s a necessity.
Let’s Improve Your Warehouse Picking Strategy
Need help reducing errors, improving fulfilment speed, or scaling up your logistics operations?
Contact the uTenant team to explore how smarter warehouse picking strategies can transform your supply chain performance.
For more information on how to optimise your picking strategies, contact the uTenant solutions team for a complimentary chat.
Updated: 23 June 2025