Improving warehouse efficiency with an optimised layout
Warehouse efficiency is crucial for businesses aiming to streamline operations and boost productivity. Whether you are designing a new warehouse or reviewing and redesigning your current one, focusing on optimising the layout of your warehouse will improve operational efficiency, streamline processes, and maximise your storage capacity.
For an existing warehouse, factors such as increased inventory needs, acquisitions, mergers, higher customer service demands, and new products, can lead to reaching storage capacity and potential operational inefficiency, if not addressed. When you face this challenge, one of the best approaches is to review and improve your warehouse layout.
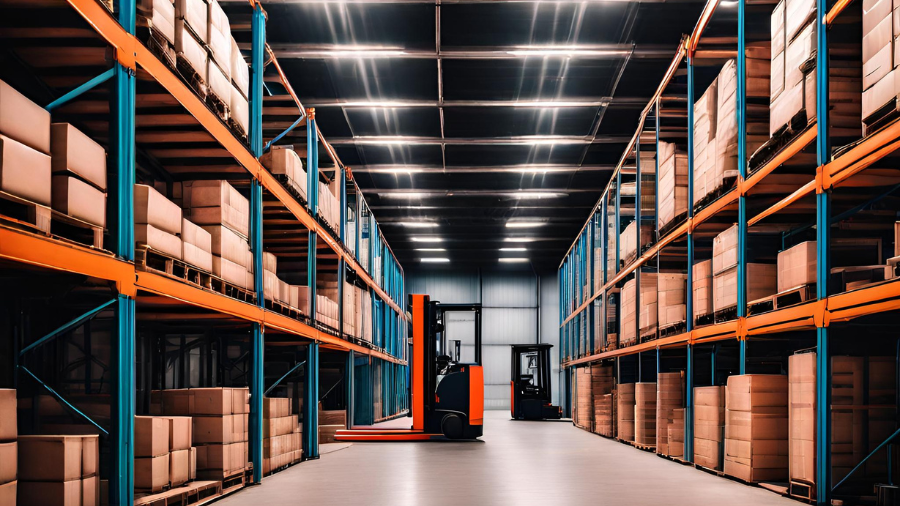
As one of the key factors influencing overall warehouse efficiency, an optimised layout can significantly improve workflow, reduce operational costs, and enhance overall productivity. In this article we will explore some practical tips and strategies to help you design and implement a warehouse layout that maximises efficiency.
1. Analysing warehouse flow
The first step in optimising a warehouse layout is to analyse the flow of goods and materials. Conduct a thorough analysis of your inventory to identify the products with high demand (therefore faster moving and higher turnover) and those that move slower.
This analysis will help you categorise items based on their frequency of use, size, and weight. Classifying products in this way allows for better strategic placement within the warehouse, and creating a warehouse layout that minimises travel time and distance of goods in a warehouse, which will improve productivity and reduce overall costs.
Additionally by employing techniques like process mapping, time-motion studies, and value stream mapping, Warehouse Managers can identify bottlenecks and streamline the flow of goods through the warehouse. The objective is to create a smooth, uninterrupted process that enhances throughput and reduces delays.
2. Embracing automation and technology
The Australian market has shown a growing appetite for automation and technology adoption in warehousing and logistics. This isn’t just a trend, it’s a strategic move that holds immense potential for optimising warehouse layouts and transforming operational warehouse efficiency.
Robotic systems and automated conveyor belts, for instance, present an opportunity to reimagine the physical layout of the warehouse. By automating repetitive and labour-intensive tasks, businesses not only reduce manual labour costs but also unlock the potential for a more streamlined and space-efficient layout.
Warehouse Managers play a pivotal role in this transformation. Assessing the specific needs and budget constraints of their operations, Warehouse Managers can strategically integrate automation technologies that align seamlessly with their existing layout. By embracing these innovations and working together with technology providers, Warehouse Managers can position their operations at the forefront of efficiency, unlocking the full potential of an optimized layout.
A collaborative partnership with Warehouse Management System (WMS) vendors becomes instrumental in this process. Warehouse Managers should view their relationship with WMS providers as more than just a transactional engagement; it's a strategic collaboration. By working closely with technology experts, warehouse managers can gain insights into tailoring the layout to accommodate automated systems effectively.
3. Utilising vertical space
When looking to optimise your warehouse layout and storage, you should consider ‘up’ (vertical) as much as ‘out’ (horizontal). Land scarcity in high demand areas and high real estate costs has made the efficient utilisation of vertical space a necessity in these areas. Given the constricted horizontal dimensions of warehouses, optimising vertical space offers a transformative solution.
Understanding your flow of goods (covered earlier in this article), to deploy systematic stacking methodologies and appropriate vertical storage systems, businesses can amplify storage capacity without expanding their physical footprint. By incorporating mezzanine floors, vertical racks, and high bay storage systems, businesses can significantly increase storage capacity (warehouse density).
Importantly, the implementation of these strategies should prioritise safety considerations, ensuring that vertical storage adheres to safety standards and guidelines. Investing in suitable equipment, such as sturdy shelving units and advanced material handling systems, not only enhances safety protocols but also contributes significantly to the overall efficiency of the warehouse.
4. Implementing cross-docking
Cross-docking is a highly effective method for streamlining supply chain operations, especially for industries that experience frequent and time-sensitive deliveries. This approach involves unloading incoming shipments from suppliers and directly loading them onto outbound trucks for distribution to customers, bypassing the need for storage.
By incorporating a staging area for cross-docking into the warehouse layout, businesses not only streamline their operational processes, but also adopt a layout that prioritises the seamless movement of goods.
While not suitable for all types of inventory, implementing cross-docking for fast-moving products can significantly reduce handling and storage costs, and improve warehouse efficiency.
5. Agile warehouse layouts
In an era where adaptability is the key to success, some businesses are redefining their warehouse layout to embrace agility. Agile warehouse layouts are emerging as a transformative strategy, offering a dynamic approach to warehouse efficiency that prioritise flexibility, responsiveness, and efficiency.
There are several key characteristics of an agile warehouse layout that enable operational efficiency:
- Modular storage systems – by incorporating modular shelving and storage systems that can easily be adjusted or reconfigured, you ensure optimal use of space without the constraints of fixed structures.
- Flexible aisle widths – the ability to alter aisle widths based on operational requirements. Narrow aisles may be suitable for high-density storage, while wider aisles can facilitate quick and efficient movement of larger goods.
- Dynamic slotting – a strategy that continually evaluates and adjusts the placement of products based on their demand patterns. This ensures that high-demand items are strategically located for faster picking and packing.
The benefits of implementing an agile warehouse layout include improved responsiveness to changing market dynamics, maximised use of available space, improved labour productivity, and reduced operational costs by allowing small and swift changes instead of large reconfigurations.
6. Adopting lean principles
The application of Lean principles can significantly impact warehouse layout optimisation. Lean methodologies focus on minimising waste, eliminating unnecessary inventory, and continuously improving processes. Typically, the first lean method which a business should implement is 5S (Sort, Set in Order, Shine, Standardise, Sustain).
Implementing the 5S system can enhance warehouse organisation, leading to smoother operations and easier visual management. 5S is a cyclical methodology, therefore resulting in continuous improvement.
In the Australian market, where supply chain disruptions due to natural disasters and global events are not uncommon, adopting Lean principles can make businesses more agile and adaptable to unforeseen challenges.
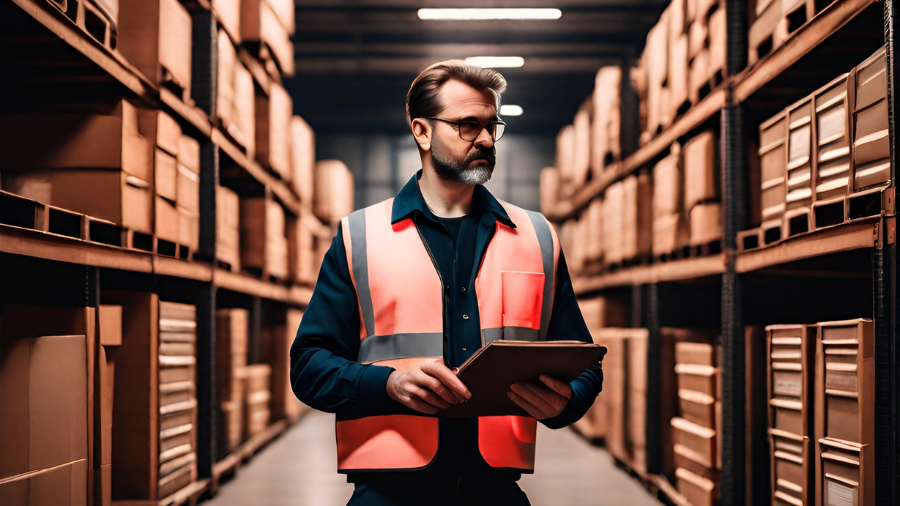
Improve warehouse efficiency to stay ahead
An optimised warehouse layout is a critical component of efficient operations. By analysing inventory, implementing warehouse picking strategies, optimising storage systems, prioritising safety, leveraging technology, and embracing a culture of continuous improvement, businesses can create a warehouse environment that maximises efficiency, reduces costs, and ultimately enhances overall productivity. Taking the time to design and maintain an efficient warehouse layout is an investment that pays off in streamlined processes, satisfied customers, and a competitive edge in the market.
Need some help?
If you need support with reviewing or improving your warehouse operations, uTenant is here to help you. With our knowledge and expertise in warehousing and supply chain solutions, we can work with you optimise your warehouse operations or find you the right 3PL partner to meet customer expectations and improve performance.
To chat to one of our solutions experts, reach out via the button below:
Published: 29 November 2023