Preparing your Supply Chain for peak season
As a supply chain manager, business owner, or third-party logistics (3PL) provider, preparing for peak season is crucial to ensure smooth operations during times of increased activity. The sudden surge in demand for products during peak season can place significant strain on resources, inventory management, and logistics. Without proper planning, supply chains can crumble under the pressure, leading to stockouts, missed deliveries, and customer dissatisfaction. Now, let’s dive into what peak season means for your business, when to expect it, and how to leverage strategies like overflow storage to handle the demands effectively.
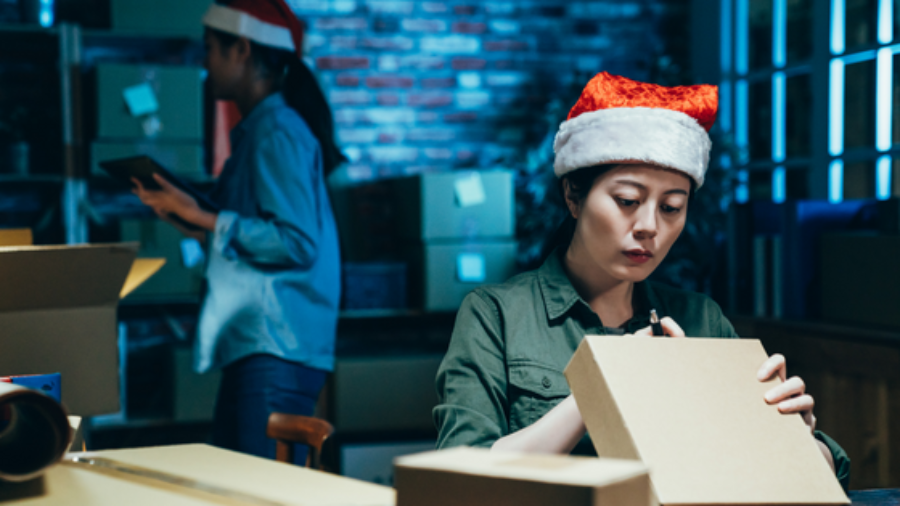
What is peak season, and how does it impact supply chains?
Peak season refers to periods during the year when demand for products significantly increases, causing a surge in inventory requirements. Common examples include the lead-up to major holidays like Easter and Christmas, Black Friday sales, and back-to-school periods. For retail and wholesale businesses, these peaks often mean higher sales volume, but they also bring logistical challenges such as managing stock levels, ensuring timely delivery, and avoiding fulfillment delays.
For product owners and brands, peak season can be a make-or-break time. A lack of preparation could result in stockouts, delayed shipments, and lost revenue. On the other hand, over-preparation can lead to excess inventory and increased storage costs. 3PL providers, who often handle the logistics for these businesses, also face unique challenges, such as limited warehouse capacity, labour shortages, and increased transportation demands.
When to expect peak season surges
Understanding the regularity of your supply chain allows you to prepare for peaks (and troughs) in demand. Peak seasons come and go throughout the year. They can be planned and prepared for with thorough knowledge, the right resources and support, and data-driven forecasting.
The timing of peak seasons varies by industry, but common periods to anticipate high demand for inventory include:
- Q4 (October–December): The holiday season, including Black Friday, Cyber Monday, Christmas, and Boxing Day generates the highest retail sales volumes for the year.
- Back-to-School (January - February): Especially impactful for retail and office supplies, clothing, and electronics.
- End of Financial Year (June–July): Some industries experience heightened demand as businesses finalise budgets or take advantage of sales events.
The major peak seasons tend to occur in the second half of the year. This means businesses have the first half of the year to thoroughly review the prior year's peak seasons, and use this data to make preparations to overcome any hurdles and be better positioned for the upcoming peak seasons. This is plenty of time to make adjustments locally, and perhaps enough time to improve the overall health of your supply chain to optimise the flow of goods.
Understanding peak season and yearly patterns will allow you to forecast your business and customer needs and plan appropriately, ensuring smooth operations and customer satisfaction.
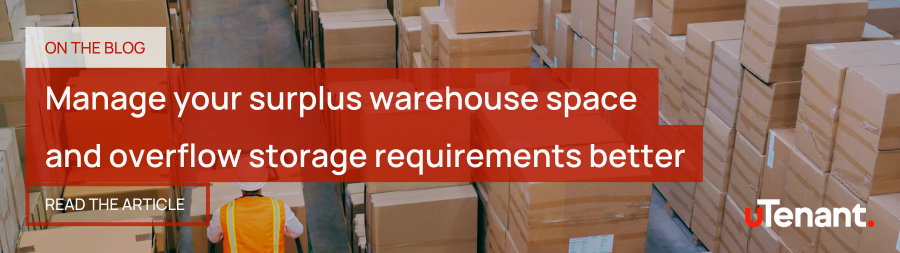
Forecasting demand for peak season
Forecasting demand is key to navigating peak season successfully. By analysing your historical sales data, market trends, and customer behavior, you can predict the volume of stock required to get through peak season, and the warehouse space required to store it, in advance. For example, retailers can look at past Q4 sales patterns, consider upcoming marketing campaigns, and evaluate the potential impact of external factors such as consumer spending habits and economic conditions.
For 3PL providers, understanding the seasonal needs of clients will allow you to plan warehouse capacity, transportation requirements, and labour resources more effectively. Working closely with your clients to forecast demand will ensure operations run as smoothly as possible during peak season. This foresight not only prevents bottlenecks in the supply chain but also allows for cost-saving measures such as early procurement of additional storage space and optimised transportation routes.
No forecast is perfect, but it's going to be much worse if you don't forecast demand for peak season. There may still be unexpected shifts in demand, whether from global events, changing consumer preferences, or supply chain disruptions. Your preparedness will determine how well you can respond. This is where additional planning and resources, such as overflow storage and flexible labour, come into play. By focusing on proactive planning, you can maintain a level of control over inventory, keep costs manageable, and meet customer expectations, all while navigating the complexities of peak season.
Overflow storage: a key solution for managing peak season
One of the most effective strategies for handling the influx of inventory during peak season is overflow storage. This concept involves securing additional warehouse space to accommodate excess stock that can't be stored in your regular facilities. Overflow storage helps ensure you have enough capacity to meet customer demand without overcrowding your main warehouse or distribution centres, and works as a solution for both product owners and 3PL providers.
For product owners, overflow storage can prevent stockouts during high-demand periods and reduce the pressure of managing limited space because you can hold more inventory onshore than you normally do. This inventory management practice is also referred to as just-in-case.
Outsourcing overflow inventory storage to a 3PL provider is a practical solution to properly managing that extra peak season inventory. A 3PL partner can act as an intermediary warehouse for your products and then ship to your primary warehouse to replenish stock for fulfilment by the pallet load, essentially keeping the flow or your goods as close as possible to your normal supply chain.

For 3PL providers, an overflow storage solution allows them to support their clients' needs without compromising service quality or operational efficiency, by securing additional capacity through a storage agreement with another 3PL provider or subleasing more warehouse space.
Finding overflow storage at short notice can be a challenge, especially when demand is high across the entire supply chain. This is where uTenant can help. As experts in sourcing overflow storage, we connect businesses and 3PL providers with the right facilities in the lead-up to peak seasons. Whether you need short-term or long-term solutions, uTenant provides tailored options to match your specific requirements.
Additional inventory management solutions during peak season
In addition to overflow storage, there are several other strategies that businesses and 3PL providers can implement to prepare for peak season:
- Demand forecasting: As mentioned earlier, using data-driven insights to predict the volume of sales and inventory needs can significantly reduce the risk of over-stocking or under-stocking during peak seasons.
- Flexible labour sourcing: Many businesses bring on additional staff during peak seasons to manage increased warehouse and logistics activities. Cross-training employees to handle various roles can also improve efficiency.
- Inventory optimisation: Implementing advanced inventory management systems can help streamline stock levels, reduce carrying costs, and ensure products are available when customers need them.
- Transportation planning: Ensuring that your transportation network can handle increased demand is crucial. Partnering with reliable carriers and securing transportation capacity early can help avoid delays and disruptions.
- Optimised warehouse layout: This improves efficiency during peak season by reducing bottlenecks, speeding up order fulfillment, and maximising storage capacity through strategic product placement and clear organisation.
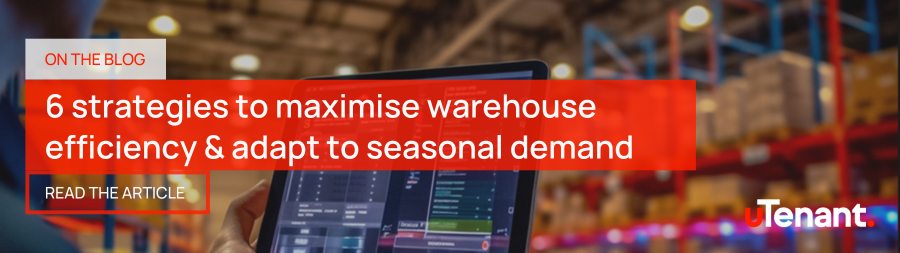
Potential consequences of not properly preparing for peak season
Part of preparing for upcoming peak seasons, is reviewing, analysing, and evaluating how your business and supply chain performed last season. If it went well, then take the aspects that worked well and ensure they are carried through to this peak season. You can also make further adjustments to ensure those aspects work even better, after all, there is always room for improvement.
If things went poorly last peak season, learn from those errors. It’s time to start asking questions across your supply chain, for example:
- Was the forecast inaccurate?
- What went wrong?
- What segments of the supply chain failed?
- When it went wrong, what solutions were used to fix it?
Warehouses without allocated overflow locations or secondary storage will end up using main floor space or staging areas to juggle inventory and orders. This may lead to inventory not being able to be tracked properly in the warehouse, leading to inefficiencies and errors in fulfillment.
In recent years, a major global event caused wide spread chaos to supply chains. COVID-19 disrupted entire global supply chains from end to end. At the start of the supply chain, manufacturing and raw materials slowed down when workers couldn’t show up for their shifts; then shipments were delayed by road, rail, and sea congestion further down the supply chain, with less available resources.
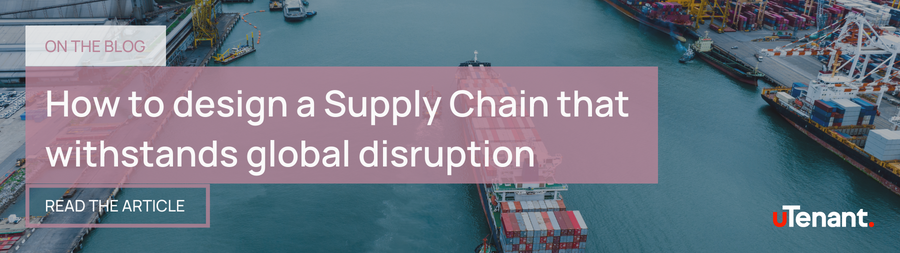
A more minor, but more regular occurrence, is holiday shutdowns. For example, Chinese New Year shutdowns have a significant impact on global supply chains, particularly for businesses that rely on manufacturing and sourcing from China. During this holiday, many factories close for up to two weeks, leading to production delays and disruptions in the flow of goods. This creates challenges in maintaining inventory levels, especially when the shutdown overlaps with key peak seasons, such as the lead-up to seasonal sales or new product launches. You must plan well in advance to avoid stock shortages, by potentially increasing orders or securing overflow storage to ensure product availability onshore during the holiday-induced slowdown.
Managing overflow of inventory caused by an influx of stock arriving as a result of over-ordering product up front for peak periods, returned products from unexpected mass returns or recalls, and backlogs of products that have yet to be shipped can be difficult. It can also have a detrimental effect on the efficiency of your operations. Simply put, overflow inventory tends to take up space that wasn't accounted for and normally means less available space in your warehouse than you wanted. So, nothing beats planning ahead. It usually also means you have the greatest number of warehousing solutions available to you, to mitigate any risk before it can arise.
How uTenant can help you prepare for peak season
Preparing for peak season requires careful planning. At uTenant, we specialise in connecting businesses with the resources they need to thrive during high-demand periods. Whether you’re a product owner in need of overflow storage or a 3PL provider looking to expand your warehousing network, we connect those looking for warehouse space, with those who have it. Finding you solutions that match your supply chain requirements.
By leveraging uTenant's extensive network of warehouse providers, we ensure you have the right space and logistics solution to manage your inventory efficiently during peak season. Don’t wait until the last minute - contact uTenant today to secure your overflow storage and make sure your supply chain is ready for peak season.
Updated: 16 September 2024