Warehouse performance: what to measure?
A well-performing warehouse is essential to ensuring the smooth operation of any business that distributes products. To maximise productivity and to maintain a competitive edge, warehouse managers must have a clear understanding of their facility's performance. How do you get a clear understanding of your warehouse's performance? You measure and track.
Key performance indicators (KPIs) are a set of measurable targets that allow you to track specific aspects of warehouse operations. By tracking operational KPIs, you can identify areas where your warehouse is performing well and areas where there is room for improvement. We’ve listed some of the important KPI’s that can provide insights into warehouse performance.
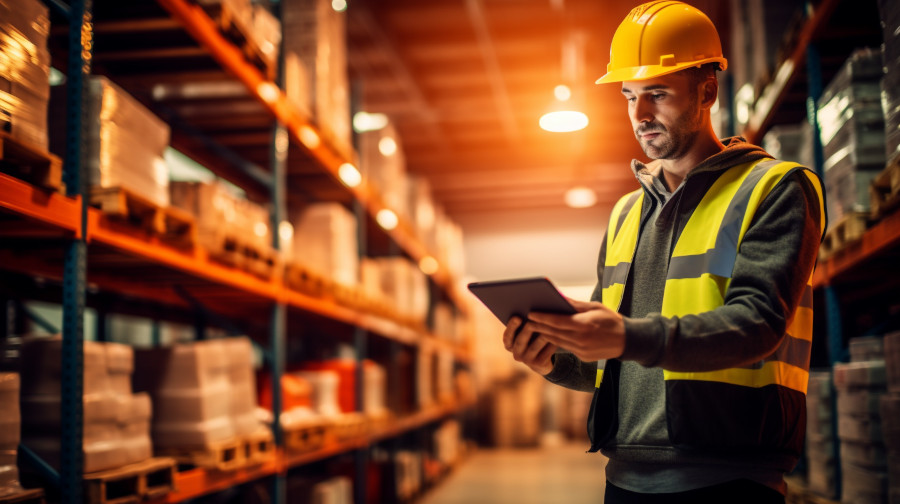
1. Order fulfillment accuracy
One of the fundamental metrics for evaluating warehouse performance is order fulfillment accuracy. It measures the percentage of orders picked, packed, and shipped correctly without errors or discrepancies. A high order fulfillment accuracy rate indicates an efficient and reliable warehouse operation, leading to satisfied customers and minimised returns or replacements.
By identifying any recurring issues such as picking errors, packaging mistakes, or shipping inaccuracies, warehouse managers are able to implement corrective measures and improve accuracy rates over time.
2. Inventory turnover
Inventory turnover is a crucial metric that determines how well an organisation manages its inventory. It calculates the number of times inventory is sold and replaced within a given period. A high inventory turnover rate suggests that products are moving quickly through the warehouse, reducing holding costs and the risk of obsolete or expired stock. As the markets slowly resumed business post the COVID-19 lockdown, this turnover has been slowing in pace, as more inventory was purchased and stocked in warehouses to mitigate against supply chain shortages due to COVID-19.
By assessing the turnover, warehouse managers can also assess the efficiency of their inventory management, identify slow-moving or excess stock, and make informed decisions to optimise stock levels and replenishment strategies.
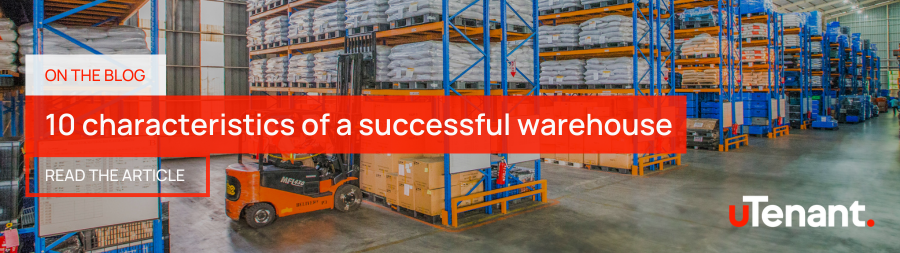
3. Cycle time
Cycle time refers to the total time it takes for an order to move through the warehouse, from the moment it is received, to when it is ready for shipment. It includes processing, picking, packing, and any additional value-added steps specific to the warehouse's operations. By measuring cycle time, warehouse managers gain insights into the efficiency of their order fulfillment processes and can identify bottlenecks or areas that require improvement.
4. Warehouse capacity utilisation
Warehouse capacity utilisation measures the percentage of available storage space that is currently being utilised. It is essential to ensure optimal use of warehouse resources and avoid overcrowding or underutilisation of storage areas. A high warehouse capacity utilisation rate indicates efficient space management, while a low rate suggests opportunities for optimisation or expansion. The majority of warehouses in Australia are designed in such a way that they enable owners to utilise the space optimally.
By tracking this metric over time, warehouse managers can identify trends, plan for future growth, and make informed decisions regarding warehouse layout, storage systems, and resource allocation.
5. Pick and pack accuracy
Pick and pack accuracy is a metric that measures the accuracy of the picking and packing process within the warehouse. It evaluates the percentage of orders that are picked and packed correctly without any errors. Tracking this metric helps identify any issues or inefficiencies in the picking and packing process, such as mispicks, incorrect quantities, or packaging errors.
By improving pick and pack accuracy, warehouses can minimise order returns, reduce customer complaints, and enhance overall operational efficiency and customer experience.
6. Downtime and equipment utilisation
Downtime refers to the time when warehouse operations are halted due to equipment breakdowns, maintenance, or other factors. Monitoring downtime and equipment utilisation metrics helps warehouse managers assess the efficiency and reliability of their equipment and identify opportunities for improvement.
By minimising downtime and optimising equipment utilisation, warehouses can reduce delays, increase productivity, and maintain a smooth workflow.
7. Labour productivity
Labour productivity is a crucial metric for measuring warehouse performance. It assesses the efficiency and output of the warehouse workforce in terms of tasks completed within a given time frame. Tracking labour productivity helps identify top performers, evaluate training needs, and optimise workforce planning.
By setting performance benchmarks, providing training and incentives, and streamlining processes, warehouses can improve labour productivity and overall operational efficiency.
8. Returns and reverse logistics
Returns and reverse logistics metrics evaluate the efficiency of handling product returns and managing the reverse supply chain. This includes measuring the percentage of returned items, processing time for returns, and the ability to resell or refurbish returned products. By monitoring these metrics, warehouses can identify trends in returns, analyse the reasons behind them, implement strategies to minimise returns, streamline reverse logistics processes, and recover value from returned items.
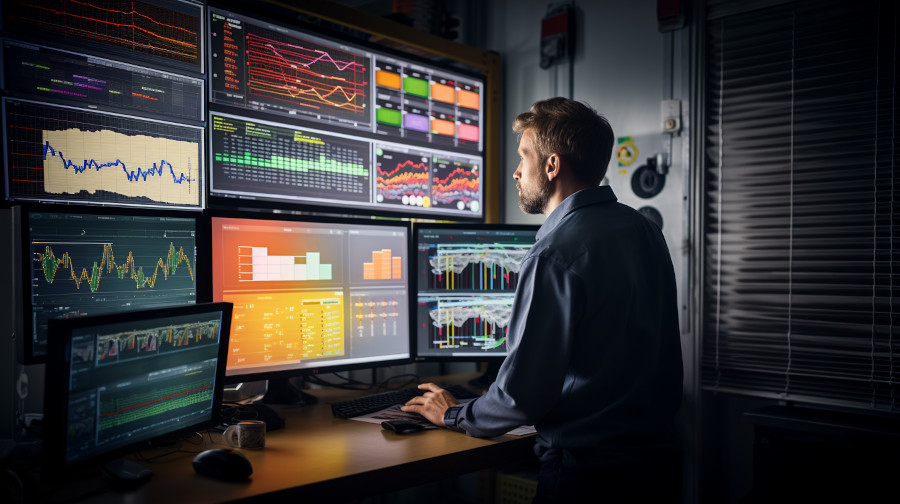
In summary
The best way to collect data on warehouse performance will depend on the size and complexity of your warehouse and the specific KPIs that you're tracking. To enable ongoing success in your warehouse operations you should:
- Collect the data on warehouse performance across the operation.
- Analyse the data against targets to identify areas where improvements can be made.
- Identify bottlenecks in your warehouse operations.
- Develop strategies for improving efficiency.
Measuring warehouse performance is an essential part of managing a successful warehouse. By tracking the right KPIs and analysing the data, you can identify areas where improvements can be made and improve the ongoing and overall efficiency of your warehouse operations.
Regular monitoring, analysis, and continuous improvement efforts based on these metrics help warehouses optimise processes, enhance customer service, and maintain a competitive edge in today's demanding business landscape.
Download a list of common KPIs for warehouse operations and their definitions.
Need some help?
If you need support with your inventory storage and management, uTenant is here to help you. With our knowledge and expertise in warehousing and supply chain solutions, we can work with you optimise your warehouse operations to meet customer expectations and improve performance.
To chat to one of our solutions experts, reach out via the button below:
Published: 1 November 2023