Everything you need to know about warehouse automation
Warehouse automation is transforming how modern supply chains operate — and it’s not just a buzzword anymore. From automated storage and retrieval systems to autonomous mobile robots, automation is helping businesses move faster, reduce costs, and improve inventory accuracy. In this guide, we’ll unpack everything you need to know about warehouse automation — the systems, technologies, trends, and how you can benefit.
TL;DR
Warehouse automation is redefining modern supply chains by improving speed, accuracy, and scalability. This guide covers the key systems and technologies—like autonomous mobile robots, automated storage and retrieval systems, voice picking, and barcode scanning—that businesses are using to reduce manual labour and streamline warehouse operations.
- Strategy first: Start with clear goals, audit your current processes, and choose scalable automation solutions that suit your needs.
- Core tech: From AGVs to machine learning-powered WMS, today’s warehouses blend physical and digital automation to maximise efficiency.
- Challenges exist: Upfront costs, system integration, and workforce reskilling require careful planning—but the long-term ROI is strong.
- Trends to watch: Cobots, green warehousing, and system interoperability are reshaping warehouse management in 2025.
- Big impact: Automation supports faster order fulfilment, improved inventory accuracy, and lower labour costs—while strengthening the entire supply chain.
Whether you're scaling for peak demand or upgrading outdated systems, warehouse automation is now essential—not optional.
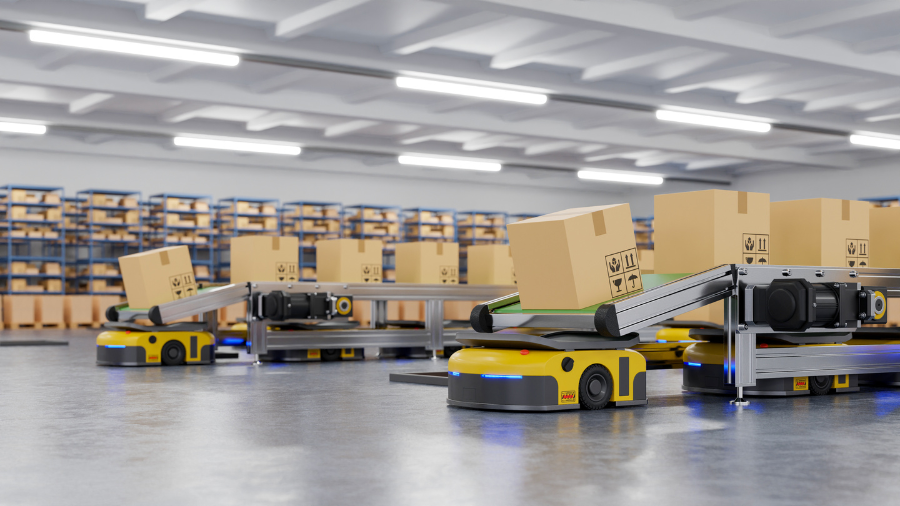
Core Components of a Successful Warehouse Automation Strategy
A successful warehouse automation plan is about creating a roadmap that aligns with your broader operational objectives. Whether you're retrofitting an existing facility or building a new automated warehouse, consider these core steps:
1. Define Objectives and KPIs
Before introducing any automation systems, clarify what success looks like. Are you aiming for faster order fulfillment? Lower labour costs? Improved inventory management? Your objectives should guide your technology investments and help track ROI.
2. Audit Current Warehouse Operations
Map out current warehouse processes and identify inefficiencies. Are pickers walking excessive distances? Are there delays in your material handling workflows? Understanding where time and resources are lost will help you prioritise areas to automate tasks.
3. Evaluate Existing Software Systems
Your warehouse management systems (WMS) and enterprise resource planning (ERP) platforms play a pivotal role. Ensure your existing software systems can support integration with automated systems like conveyor systems, voice picking technologies, or robotic pickers. A flexible WMS is essential to orchestrating your entire warehouse floor.
4. Choose Scalable Automation Solutions
Not every facility needs a full overhaul. For some, implementing put to light systems, barcode scanning, or voice picking systems may offer enough efficiency gains. For others, high-throughput environments may require automated storage and retrieval systems (AS/RS) or automated sortation systems.
5. Plan for Change Management
A well-executed automation warehouse project includes training programs for warehouse managers, clear communication with warehouse workers, and proactive engagement to maintain morale. Manual processes won’t disappear overnight — they’ll evolve alongside technology.
6. Build a Maintenance and Support Plan
To ensure long-term success, schedule ongoing maintenance and implement predictive maintenance tools that alert managers before failures occur. This reduces downtime and protects your investment in automated equipment.
Common Automation Technologies in Use Today
From physical robotics to smart software, warehouse automation technology spans a wide spectrum. Below are some of the most widely adopted tools in use today.
Automated Guided Vehicles (AGVs)
Perfect for structured environments, AGVs follow fixed paths using magnets or lasers. They're ideal for transporting goods across predictable routes and reducing manual labor in material handling tasks.
Autonomous Mobile Robots (AMRs)
Unlike AGVs, autonomous mobile robots use sensors and AI to adapt their navigation in real time. These mobile robots are a go-to choice for e-commerce and 3PL operations dealing with high SKU variability and dynamic layouts.
Automated Storage and Retrieval Systems (AS/RS)
Automated storage and retrieval systems maximise vertical warehouse space while increasing picking speed. These systems are often integrated with warehouse management software to monitor inventory levels and improve inventory accuracy.
Barcode Scanners and RFID
Barcode scanning and radio frequency identification (RFID) are essential for tracking inventory and reducing shrinkage. They provide real-time visibility and enable better inventory control, particularly when integrated with digital automation platforms.
Voice Picking and Put-to-Light Systems
Used by major retailers and ecommerce players, voice picking systems guide workers through pick tasks via voice commands, improving accuracy and speed. Similarly, put to light systems use illuminated indicators to direct items to the correct bin or order.
Machine Learning and Artificial Intelligence
Today’s advanced technologies include machine learning algorithms for demand forecasting, warehouse heat mapping, and performance analytics. Combined with artificial intelligence, these tools help predict outages, optimise space, and streamline overall warehouse operations.
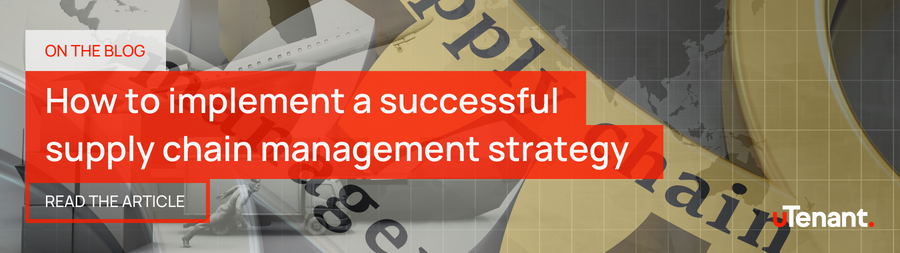
Overcoming Challenges in Warehouse Automation
Even with the clear benefits of warehouse automation, implementation comes with its own set of challenges. Understanding these pain points helps ensure a smoother transition and long-term success.
High Upfront Costs
One of the most common concerns is the high capital investment required for automation. Automated warehouse solutions — from automated guided vehicles to full-scale automated storage and retrieval systems — can be expensive to install and configure.
However, these costs often deliver strong ROI when measured against labour costs, operational inefficiencies, and long-term cost savings. Many businesses opt to start with modular systems or partial automation, scaling up as savings begin to materialise.
System Integration
Introducing new automation solutions means ensuring compatibility with existing software systems, particularly your warehouse management systems. Misaligned systems can disrupt warehouse operations, create bottlenecks, or generate inaccurate inventory control data.
To reduce risk, work with vendors that offer flexible APIs, integration support, and proven experience in linking automated systems with WMS and ERP platforms.
Labour Market Shifts
While automation reduces the reliance on manual labour, it doesn’t eliminate human input entirely. There's now a greater demand for warehouse operators who can oversee robotic automation, interpret analytics, and maintain automated equipment.
Upskilling existing warehouse workers is essential. Roles will shift from pickers and packers to technicians, trainers, and system analysts. Investing in workforce training helps maintain morale and productivity during automation rollouts.
Data Security and Cyber Risk
As warehouse automation technology becomes more connected, cybersecurity becomes a key concern. Unprotected systems can expose inventory data, order information, and even facility operations to cyber threats.
Ensure your automation warehouse solutions include secure cloud platforms, encrypted data transfers, and strict user access controls. Don’t overlook this area — especially when using machine learning or cloud-based warehouse management platforms.
Emerging Warehouse Automation Trends
As the logistics landscape evolves, several warehouse automation trends are shaping the future of global and Australian supply chains. These trends are being driven by the demand for efficient operations, workforce challenges, and the pursuit of continuous improvement in order fulfillment and inventory accuracy.
1. Rise of Collaborative Robots
Known as cobots, collaborative robots are designed to work safely alongside human workers. Unlike traditional industrial robots, cobots are flexible, mobile, and easy to program. More warehouses are deploying cobots for repetitive, ergonomically challenging tasks like sorting, picking, and packing. This blend of human oversight and robotic precision helps reduce errors and improve overall quality control.
2. Addressing Labour Shortages
Ongoing labour shortages are prompting companies to accelerate automation adoption. From mobile robots to automated guided vehicles, automation helps fill gaps in roles that are difficult to hire for—particularly in regional or high-turnover locations. This shift is also enabling reskilling of warehouse operators into supervisory or technical roles.
3. Increased Focus on System Interoperability
Businesses are demanding warehouse automation systems that integrate seamlessly with WMS, ERP, and transport management platforms. The trend is toward open architecture systems that allow modular expansion and communication across various automated equipment types.
4. Shift Toward Energy Efficiency and Green Warehousing
Sustainability continues to influence design choices. Companies are now investing in energy-efficient automation solutions, including warehouse drones, low-power automated sortation systems, and AI-optimised warehouse layout planning to reduce energy and fuel usage.
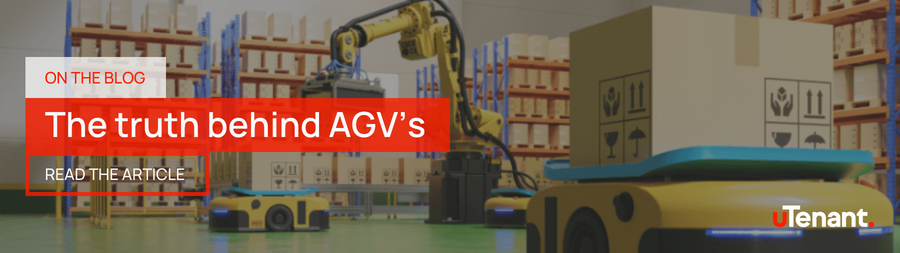
Overcoming Challenges in Warehouse Automation
Even with the clear benefits of warehouse automation, implementation comes with its own set of challenges. Understanding these pain points helps ensure a smoother transition and long-term success.
High Upfront Costs
One of the most common concerns is the high capital investment required for automation. Automated warehouse solutions — from automated guided vehicles to full-scale automated storage and retrieval systems — can be expensive to install and configure.
However, these costs often deliver strong ROI when measured against labour costs, operational inefficiencies, and long-term cost savings. Many businesses opt to start with modular systems or partial automation, scaling up as savings begin to materialise.
System Integration
Introducing new automation solutions means ensuring compatibility with existing software systems, particularly your warehouse management systems. Misaligned systems can disrupt warehouse operations, create bottlenecks, or generate inaccurate inventory control data.
To reduce risk, work with vendors that offer flexible APIs, integration support, and proven experience in linking automated systems with WMS and ERP platforms.
Labour Market Shifts
While automation reduces the reliance on manual labour, it doesn’t eliminate human input entirely. There's now a greater demand for warehouse operators who can oversee robotic automation, interpret analytics, and maintain automated equipment.
Upskilling existing warehouse workers is essential. Roles will shift from pickers and packers to technicians, trainers, and system analysts. Investing in workforce training helps maintain morale and productivity during automation rollouts.
Data Security and Cyber Risk
As warehouse automation technology becomes more connected, cybersecurity becomes a key concern. Unprotected systems can expose inventory data, order information, and even facility operations to cyber threats.
Ensure your automation warehouse solutions include secure cloud platforms, encrypted data transfers, and strict user access controls. Don’t overlook this area — especially when using machine learning or cloud-based warehouse management platforms.
Emerging Warehouse Automation Trends
As the logistics landscape evolves, several warehouse automation trends are shaping the future of global and Australian supply chains. These trends are being driven by the demand for efficient operations, workforce challenges, and the pursuit of continuous improvement in order fulfillment and inventory accuracy.
1. Rise of Collaborative Robots
Known as cobots, collaborative robots are designed to work safely alongside human workers. Unlike traditional industrial robots, cobots are flexible, mobile, and easy to program. More warehouses are deploying cobots for repetitive, ergonomically challenging tasks like sorting, picking, and packing. This blend of human oversight and robotic precision helps reduce errors and improve overall quality control.
2. Addressing Labour Shortages
Ongoing labour shortages are prompting companies to accelerate automation adoption. From mobile robots to automated guided vehicles, automation helps fill gaps in roles that are difficult to hire for—particularly in regional or high-turnover locations. This shift is also enabling reskilling of warehouse operators into supervisory or technical roles.
3. Increased Focus on System Interoperability
Businesses are demanding warehouse automation systems that integrate seamlessly with WMS, ERP, and transport management platforms. The trend is toward open architecture systems that allow modular expansion and communication across various automated equipment types.
4. Shift Toward Energy Efficiency and Green Warehousing
Sustainability continues to influence design choices. Companies are now investing in energy-efficient automation solutions, including warehouse drones, low-power automated sortation systems, and AI-optimised warehouse layout planning to reduce energy and fuel usage.
The Role of Warehouse Automation in Supply Chain Operations
As eCommerce, global sourcing, and omnichannel fulfilment continue to expand, the warehouse has become a strategic node in the supply chain — not just a storage facility. That’s where warehouse automation technology makes its biggest impact.
Automated warehouses enable companies to keep up with rapid shifts in demand, tighter delivery timeframes, and the rising cost of manual labour. Whether it’s automated storage, real-time inventory control, or robotics that enable 24/7 picking, automation reduces friction at critical points in the supply chain.
Modern warehouse automation systems can integrate directly with upstream and downstream software — including order management systems, inventory forecasting tools, and transport management platforms. This creates end-to-end visibility and enables proactive decision-making.
For example:
- Mobile robots can automatically replenish pick zones in real time to support fulfilment spikes.
- AI-based WMS platforms can sync with demand forecasts to automate replenishment planning.
- Barcode scanners and RFID tools feed live data into central dashboards that optimise distribution and reduce mispicks.
In short, successful warehouse automation doesn’t just benefit operations internally—it strengthens the entire supply chain network, enabling businesses to move faster, reduce labour costs, and meet rising customer expectations with confidence.
Real-World Applications of Warehouse Automation
Warehouse automation isn’t theoretical — it’s already transforming operations across industries. Here are just a few examples of how businesses are deploying automated systems to gain an edge:
Retail: Improving Order Fulfilment and Accuracy
In the retail sector, speed and accuracy are everything. Chains like Woolworths and Coles are investing in automated sortation systems, voice picking systems, and barcode scanners to streamline picking and packing. These technologies reduce fulfilment errors and enable faster turnaround, especially for online orders.
With the demand for near-instant order fulfillment, automation allows retailers to increase throughput without expanding their physical footprint.
Manufacturing: Optimising Material Handling and Safety
Manufacturers are using conveyor systems, AGVs, and warehouse drones to improve material handling across the production line. Automation reduces workplace injuries, cuts down on travel time between stations, and improves inventory accuracy with RFID and smart sensors.
Predictive analytics also plays a growing role, enabling predictive maintenance that prevents costly downtime from equipment failure.
E-Commerce: Scaling for Peak Periods
Ecommerce businesses often experience major fluctuations in demand, particularly during sales events or holiday periods. To cope, many are adopting autonomous mobile robots, automated storage, and put to light systems that support fast, scalable fulfilment.
Companies like Amazon have set the standard, but smaller players are following suit using modular automation solutions that reduce overhead while improving delivery speed.

Is Full Automation Right for You?
Not every facility needs to become a fully automated warehouse to gain meaningful efficiency. For many small to mid-sized businesses, partial automation—like voice picking systems, barcode scanning, or a compact automated sortation system—offers major value without the complexity or cost of enterprise-level solutions.
A good rule of thumb is to automate the most repetitive or error-prone warehouse processes first. These typically include:
- Picking and packing
- Tracking inventory
- Inventory management across multiple zones
- Internal movement of goods on the warehouse floor
As your operation grows, it becomes easier to justify investments in advanced systems like autonomous mobile robots or automated storage and retrieval systems (AS/RS).
Facilities dealing with high SKU volumes, fluctuating demand, or limited warehouse space are often ideal candidates for full-scale warehouse automation systems. However, if your current bottlenecks involve manual scanning, inefficient routing, or delayed order fulfillment, targeted automation solutions can still drive a measurable impact.
Physical vs. Digital Automation: What’s the Difference?
Understanding the distinction between physical automation and digital automation is essential when planning your automation strategy. While both aim to improve efficiency and reduce reliance on manual labour, they target different layers of warehouse operations.
Physical Automation
Physical automation involves the use of machines and robotics to perform repetitive tasks traditionally carried out by human workers. This includes:
- Automated guided vehicles (AGVs) that move pallets or materials across the warehouse floor
- Conveyor systems for fast, uninterrupted item movement
- Automated storage and retrieval systems (AS/RS) for vertical space optimisation
- Put to light systems and voice picking tools that guide staff through pick-pack tasks
These automation systems are typically more capital intensive but deliver fast returns through reduced operational costs, improved throughput, and fewer workplace injuries.
Digital Automation
On the other hand, digital automation focuses on improving data flow and decision-making. It’s about streamlining information processes using software and smart technologies. Key tools include:
- Warehouse management systems (WMS) and ERP platforms
- Barcode scanning and radio frequency identification (RFID) for tracking inventory
- Artificial intelligence and machine learning algorithms for predictive analytics, maintenance alerts, and order optimisation
When used together, physical and digital automation automate tasks at every level—creating a smarter, faster, and more scalable automation warehouse.
Most modern facilities adopt a hybrid approach, combining physical tools (like mobile robots) with digital platforms that enable seamless coordination and real-time visibility.
How to Start Warehouse Automation
Whether you’re exploring digital automation or looking to upgrade physical systems, the path to automation should be strategic and scalable. Here’s how to get started:
1. Audit Your Current Operations
Identify where manual processes are slowing your team down. Focus on high-frequency tasks, inefficiencies in inventory control, or areas where accuracy errors are creating downstream issues.
2. Set Clear Automation Goals
Define your success metrics. Are you aiming for faster warehouse operations, better inventory accuracy, reduced labour costs, or smarter warehouse layout utilisation?
Your goals will determine whether you start with conveyor systems, barcode scanners, or more sophisticated tools like robotic automation or AI-based forecasting platforms.
3. Consult Automation Experts
Not all automation warehouse setups are created equal. Speak with providers who understand your industry and offer customisable options. Look for experience in integrating new systems with your warehouse management systems or existing software systems.
4. Choose the Right Technology Stack
Based on your goals and budget, determine which technologies are most impactful:
- Autonomous mobile robots for dynamic picking
- Put to light systems for scalable ecommerce fulfilment
- Predictive maintenance sensors for reducing downtime
- Radio frequency identification (RFID) for real-time visibility
Ensure your choices support future growth and integrate easily with your broader supply chain network.
5. Train Your Team for Success
Human adoption is key to the success of any automation systems. Invest in training programs to help warehouse managers, technicians, and warehouse workers transition into new roles, operate automated equipment, and manage systems confidently.
Automate Your Warehouse with uTenant
Warehouse automation is no longer a futuristic concept—it’s a competitive necessity. Whether you're running a local fulfilment centre or a national logistics hub, adopting the right automation solutions can help you improve accuracy, reduce costs, and scale with confidence.
At uTenant, we help businesses connect with warehouse providers that support modern automation warehouse needs—from high-tech facilities to flexible warehouse management integrations.
Let’s make it happen. Contact the uTenant team today and start building the automated warehouse of tomorrow—today.
Published: 23 August 2021
Updated: 23 June 2025